Plant History
1928
In the 1920s, the USSR embarked on industrialization. The gigantic construction that was underway in the country required large volumes of building materials. In 1928, construction of the Sukhoy Log Integrated Plant began in the Ural (now Sverdlovsk) Region, which included cement, fireclay, slate, lime plants, and the Belaya Glina mine.
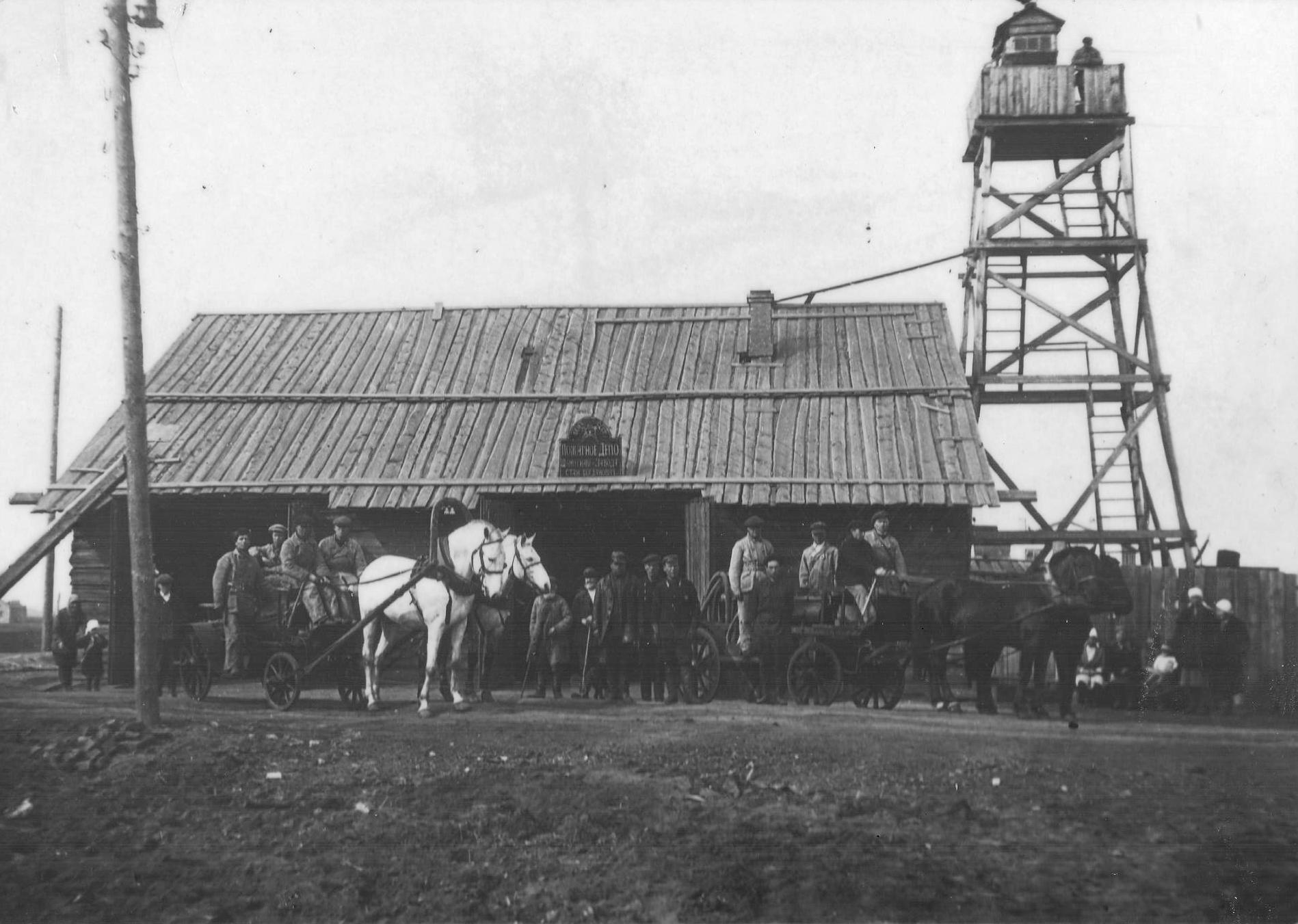
1930
In 1930, construction of the Sukhoy Log Fireclay Plant commenced. According to the Central Archives of the National Economy of the USSR, the Sukhoy Log Fireclay Plant was constructed among the first 37 enterprises in the Urals subject to mandatory commissioning in the first five-year plan, so the plant was erected ahead of schedule in order to provide refractories to the heavy industry enterprises being built.
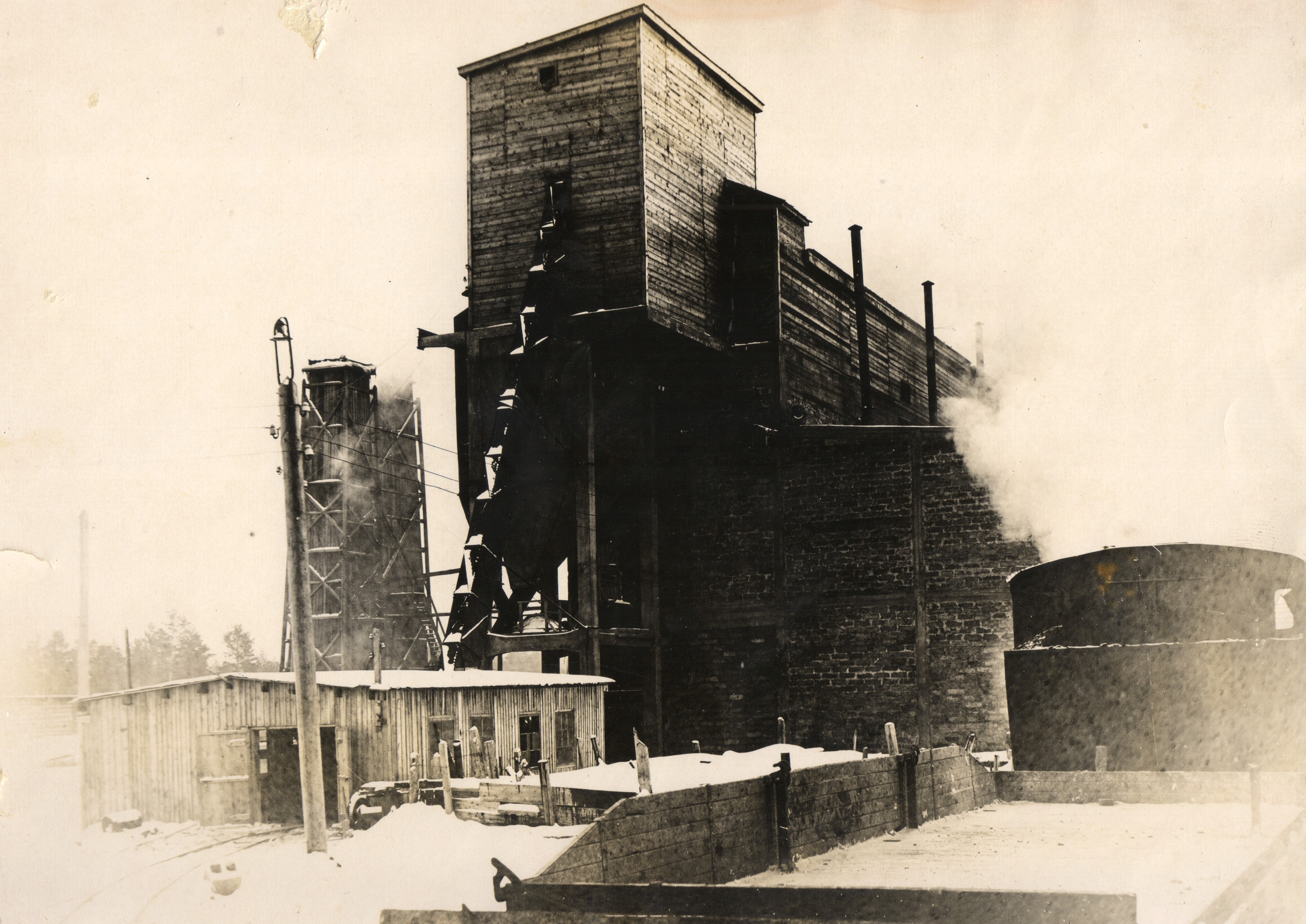
1931
Concurrently with the construction works, equipment installation was performed. The fireclay plant equipment was supplied from Germany, so the installation was carried out under the supervision of German experts. The following units were constructed: Khirta No. 1 tunnel kiln, ball mill No. 1, drying drum No. 1, auger extruder No. 1 with Ruchaud presses No. 1-2, 19-way dryers and chambers, shaft kilns designed by engineer Gross, gas generator station.
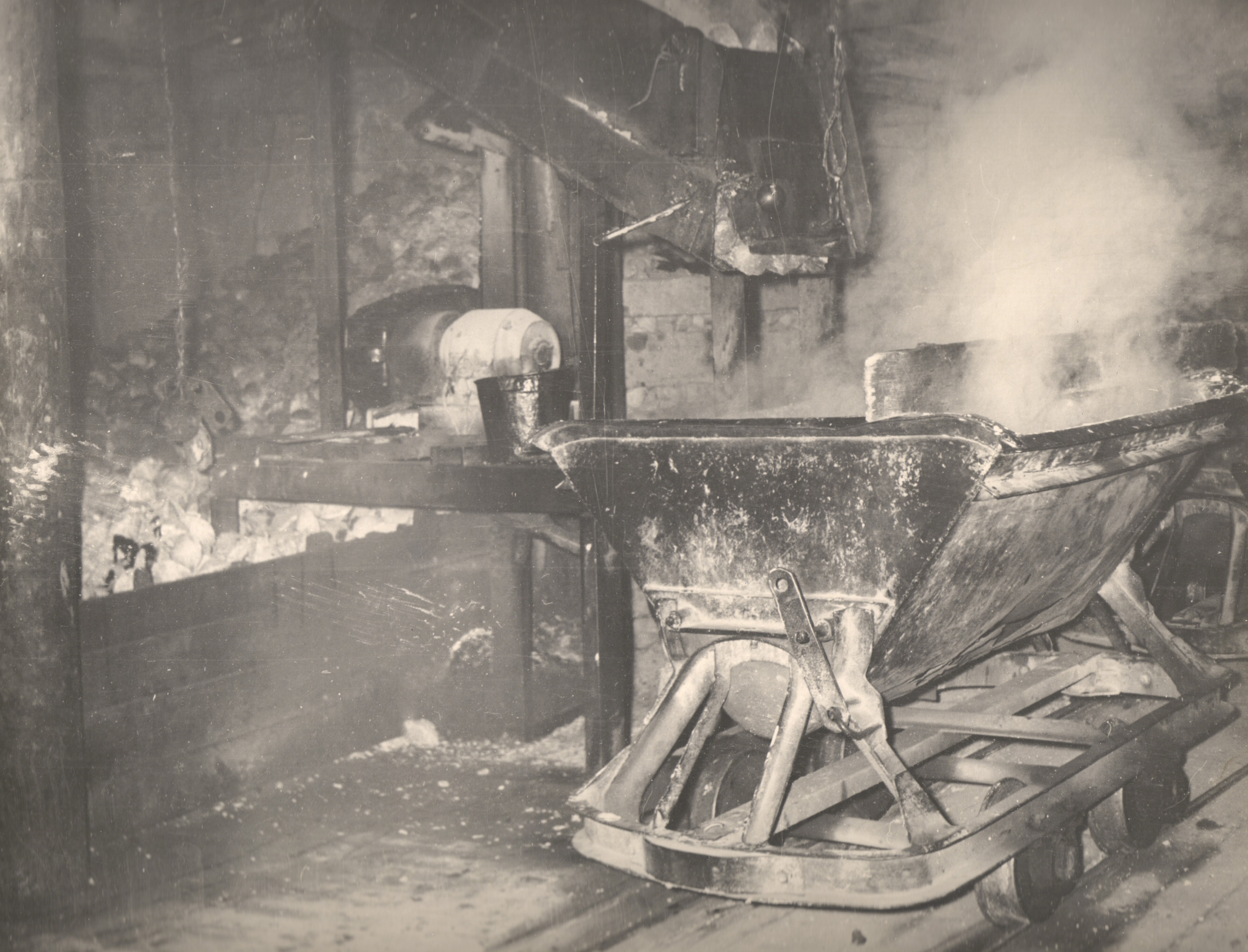
1932
On March 27, 1932, the first plant in the Urals and the east of the country producing fireclay refractory products was put into operation. By the late 1932, 6,752 tons of refractory products were produced, including 234 tons of ordinary shapes. For the first three years, the plant produced only fireclay products, and in the fourth year, the production of casting pit refractories for bottom casting was mastered.
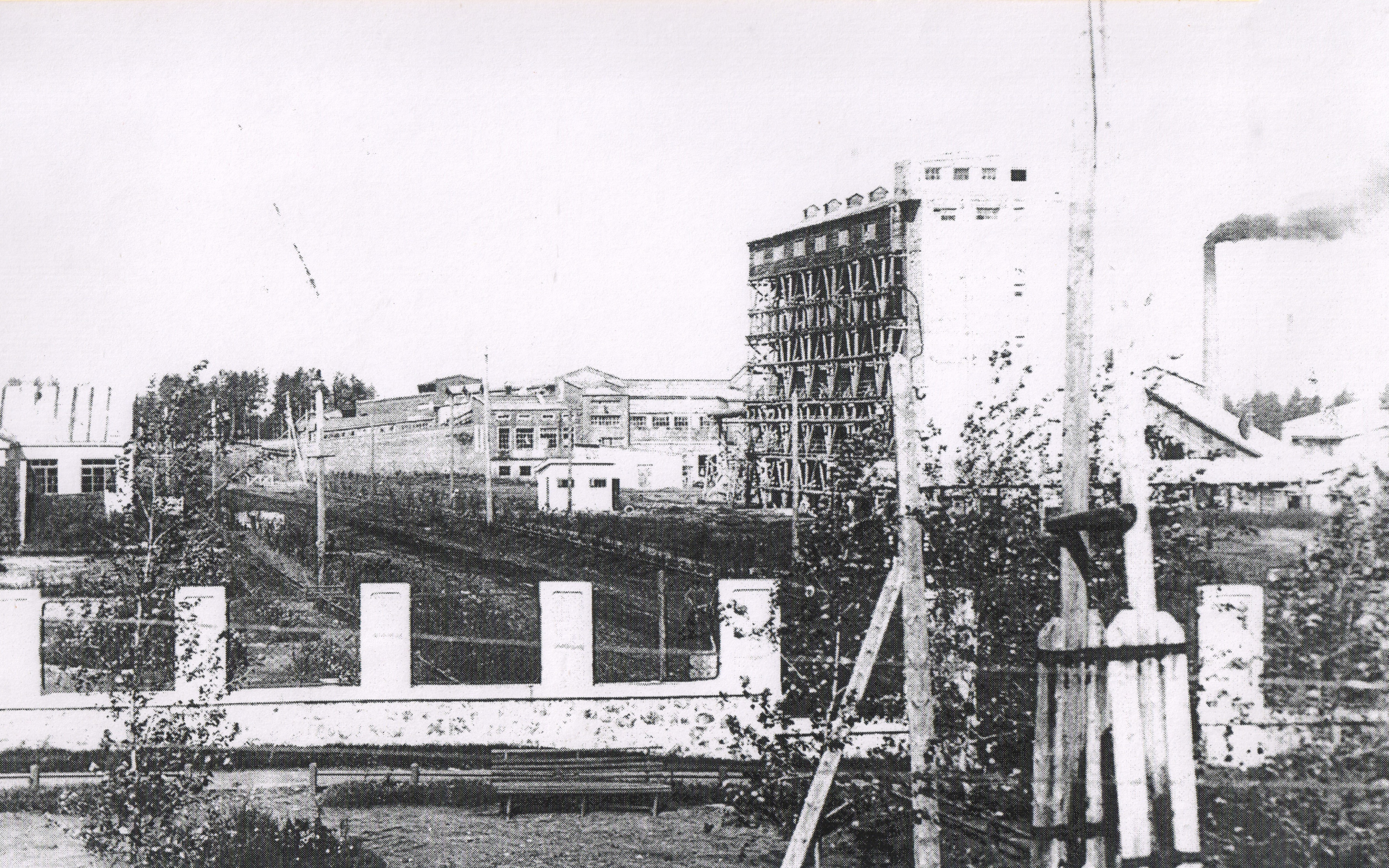
1933-1934
In 1933, the plant was already operating at full capacity. 14.6 thousand tons of refractories were produced. In 1934, the 2nd Khirta tunnel kiln was put into operation. Due to its launch, the volume of refractory production increased to 26 thousand tons per year. The plant utilized German equipment: Raupach and Ruchaud presses, as well as Berper crushers.
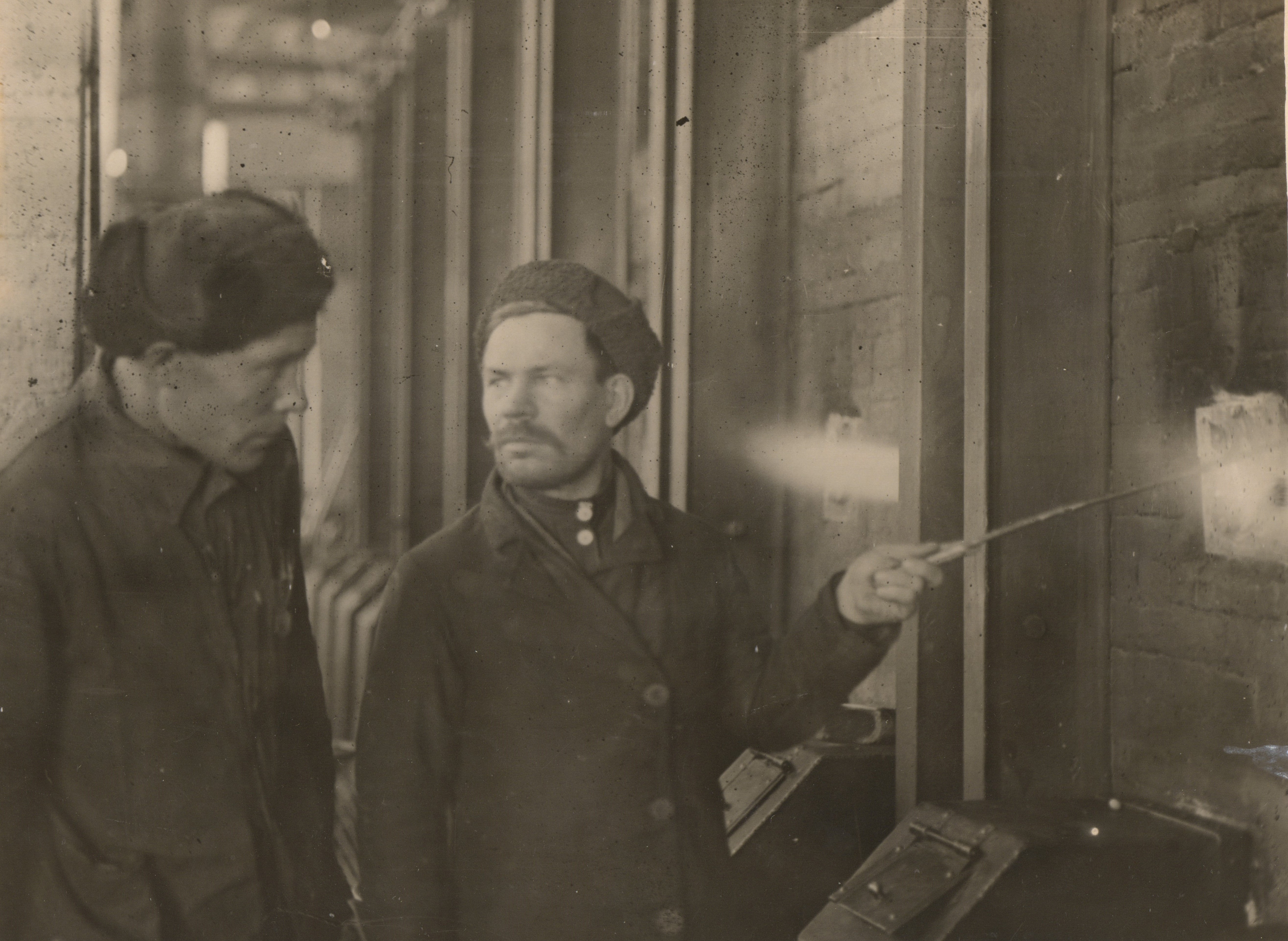
1935-1940
In 1935, 3 thousand tons of Cowper bricks for blast furnace air heaters were shipped to the Magnitogorsk Iron and Steel Works (aka Magnitka) alone. In 1940, the second line of the moulding shop was built and put into operation; production output reached 51.9 thousand tons of refractories, the increment in output compared to 1938 was 31.0%.
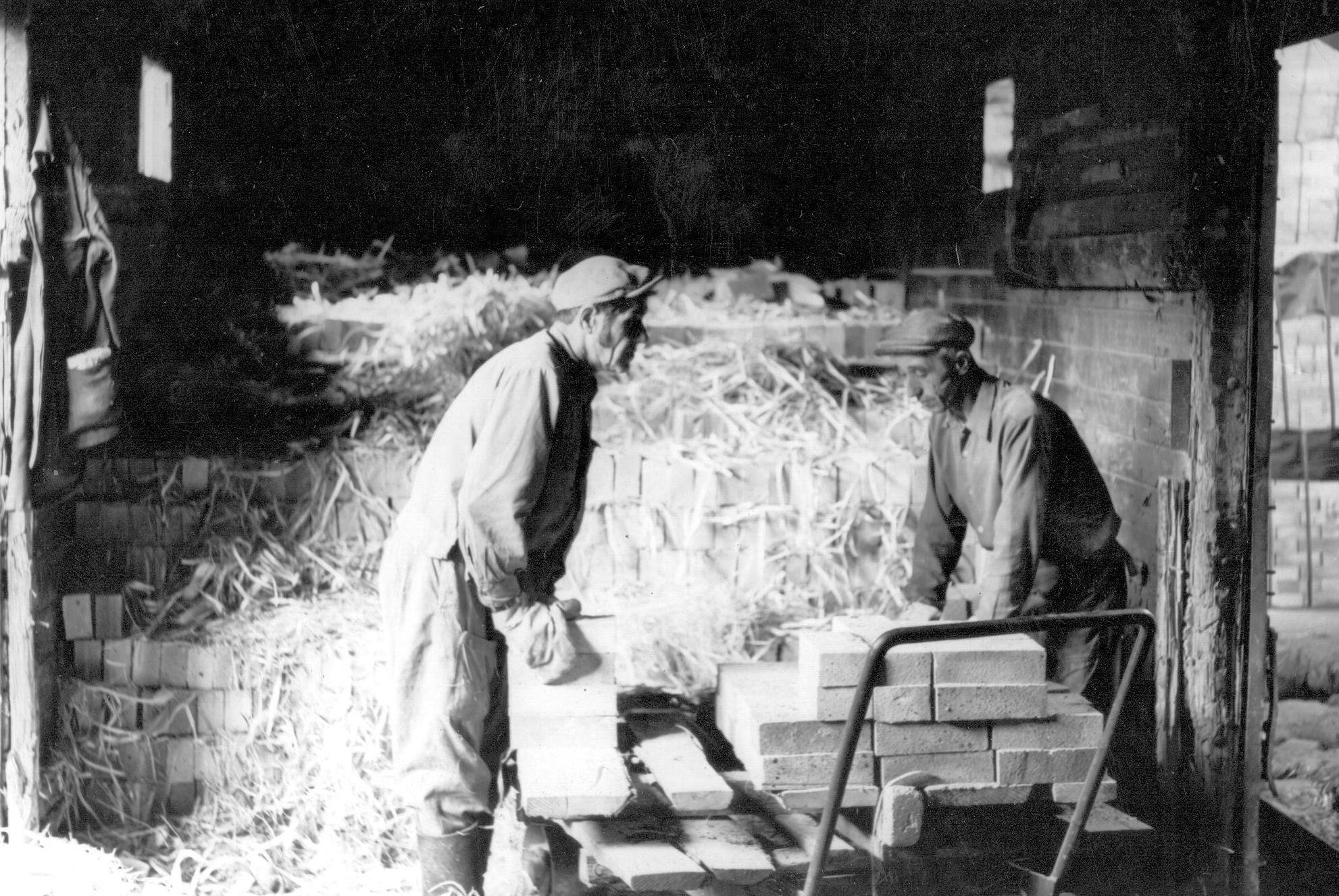
1941-1943
Over the harsh years of the Great Patriotic War, when many of the country's refractory enterprises found themselves in territories temporarily occupied by the enemy, the plant's personnel had to solve the problems of mastering and increasing the production of many complex types of refractory products within the shortest time possible. The plant construction went on: drying drum No. 2 and ball mill No. 2 in the grinding shop, as well as two annular furnaces in the furnace shop were put into operation.
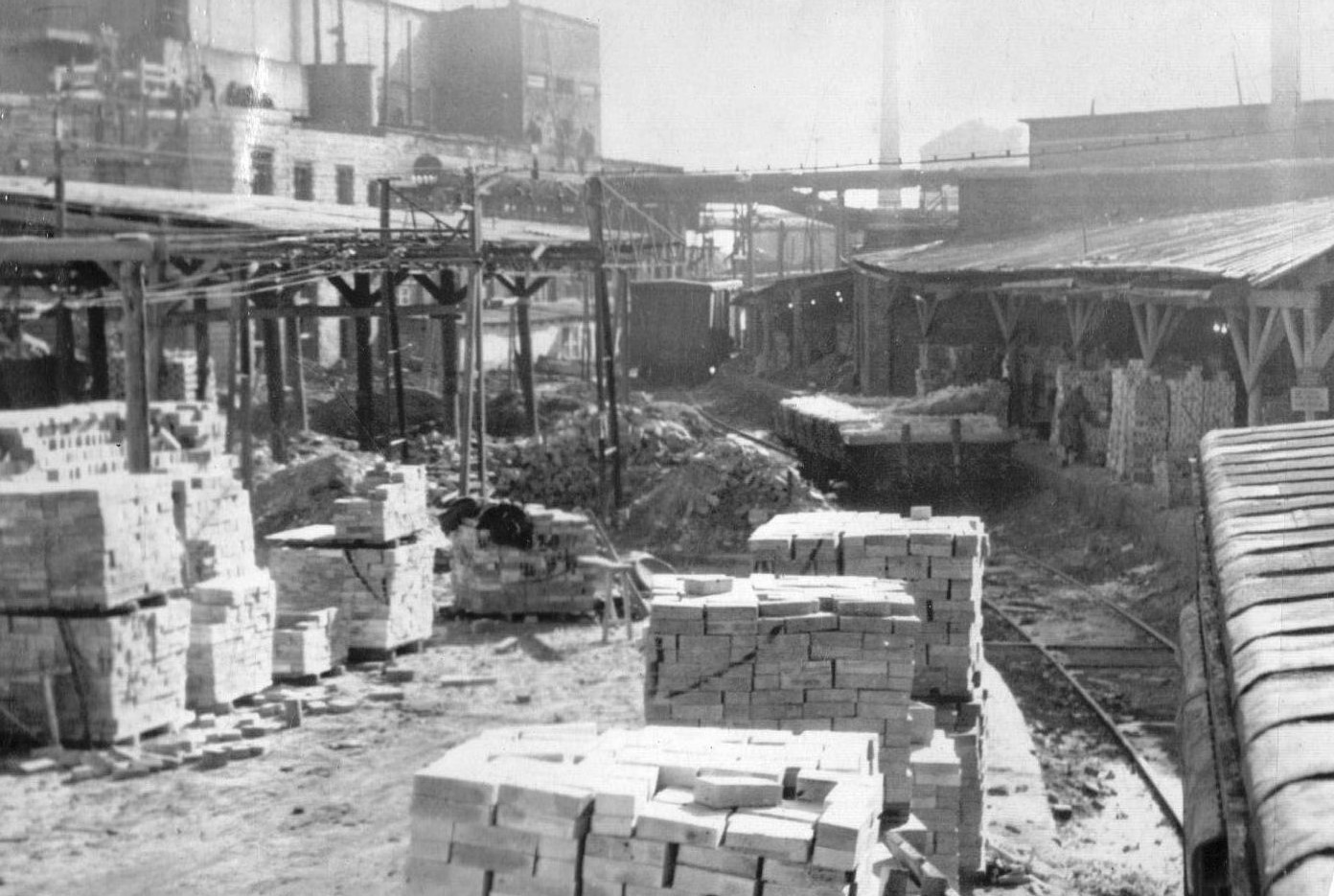
1943-1945
On the orders of the State Defense Committee, in 1943 the plant personnel quickly set up mass production of refractories for the construction of the sixth blast furnace at Magnitka. Trains with hot air bricks were sent out days and nights right on time. All plant workers took part in loading the refractories. On December 23, 1943, Magnitka's sixth blast furnace produced its first cast iron.
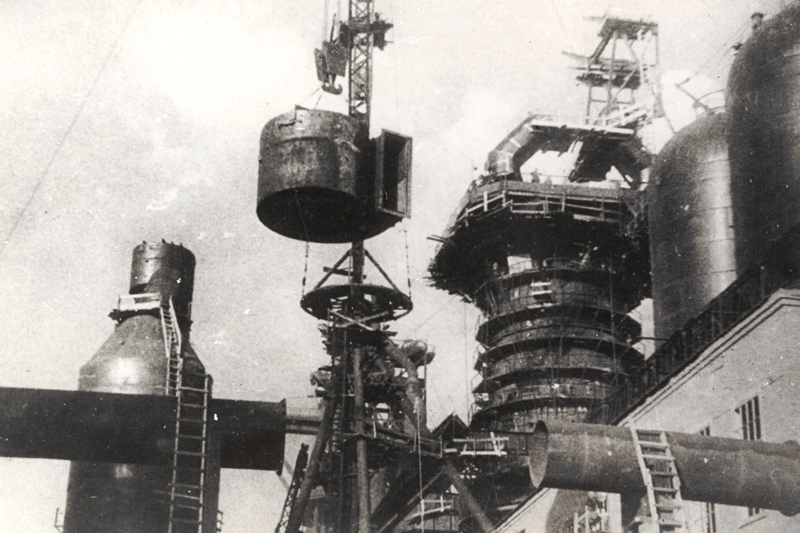
1946-1950
The plant equipment capability increased from year to year. In 1947-1949, drying drum No. 3 and ball mill No. 3, as well as clay and fireclay flow line No. 2 were put into operation in the grinding shop. The Sukhoy Log refractory men successfully fulfilled the production plan by the end of the fourth five-year plan (the number of personnel during those years was 1,360 people). The country's metallurgical industry received 429.8 thousand tons of refractory products.
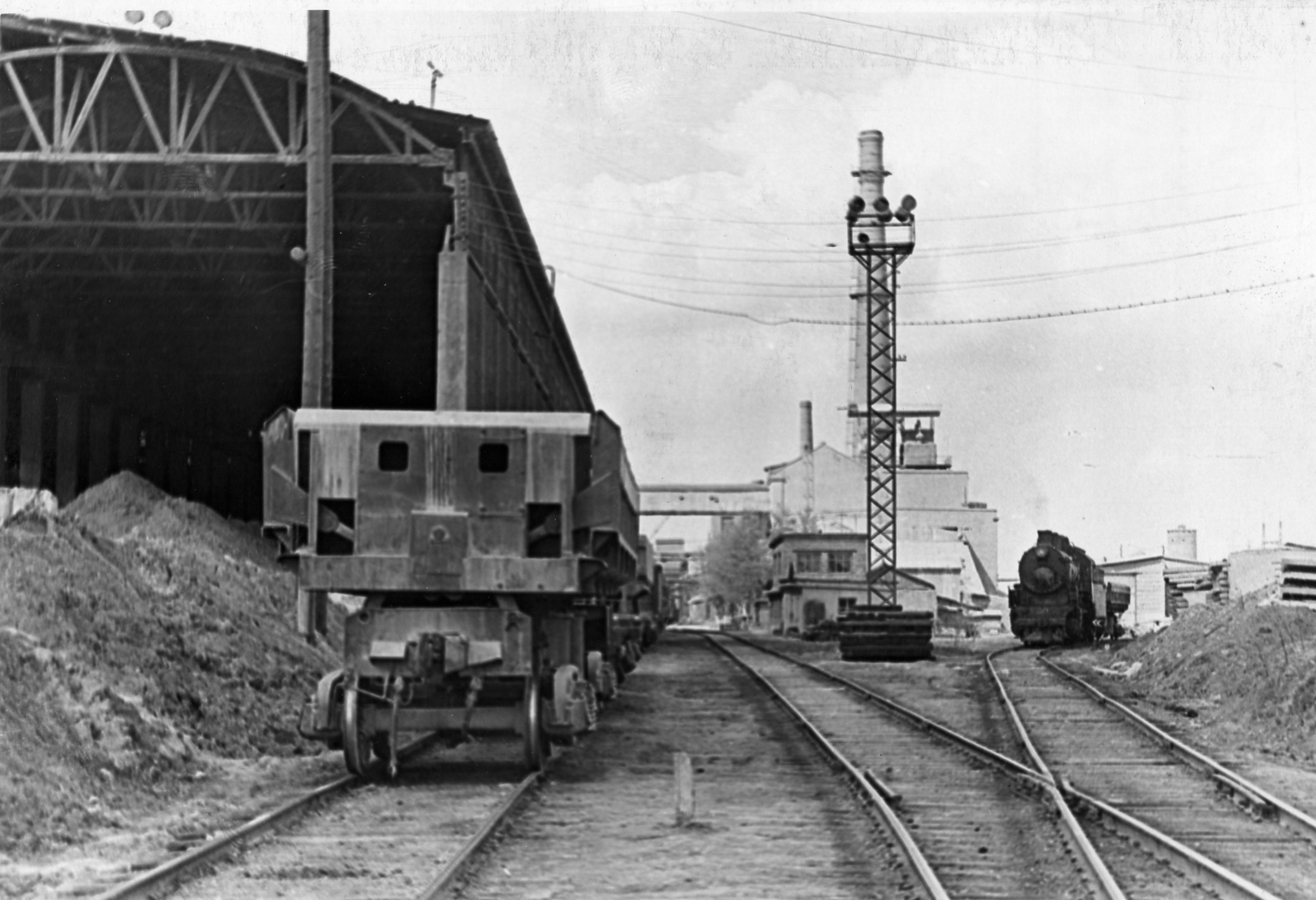
1951-1955
For the fifth five-year plan, the fireclay plant personnel tasks were closely connected with the construction of large metallurgical enterprises in the USSR. Significant expansion of refractory production lied ahead. Addressing these issues required the introduction of additional production areas, reconstruction of old ones, mastering new processes, and introducing advanced equipment.
The personnel managed to complete the fifth five-year plan and the tasks set for production development. The country's metallurgists received 718.6 thousand tons of refractories. The production output in 1955 increased by 175% compared to 1951, and by 167%, or 289 thousand tons, compared to the results of the previous five-year plan.
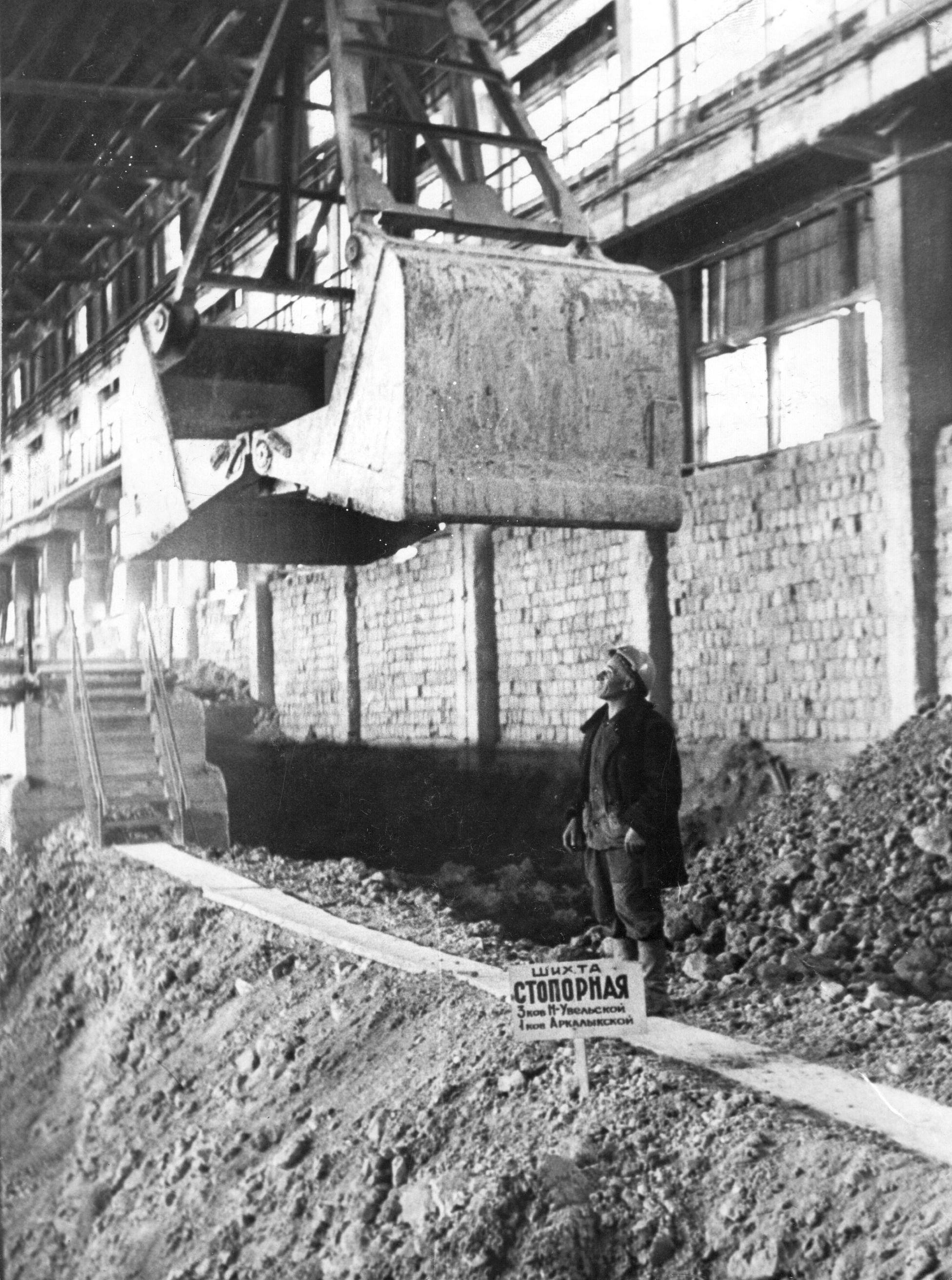
1956-1964
Over five years, the production of Sukhoy Log refractories increased by over 1.5 times (amounting to 1,106.2 thousand tons), the cost of production was reduced, and the production of new types of products was mastered. Improvements in production and technology continued. The drying drum No. 4, ball mill No. 4, tunnel dryers, and semi-dry pressing lines were put into production. The construction of the 3rd clay flow line with two disintegrators was underway.
A new mechanical shop and a plant boiler house were erected. In 1962, a complete reconstruction of the grinding and crushing department was carried out, a semi-dry pressing shop was put into operation, and the gas furnace (calcinating) shop with tunnel kilns was completely upgraded.
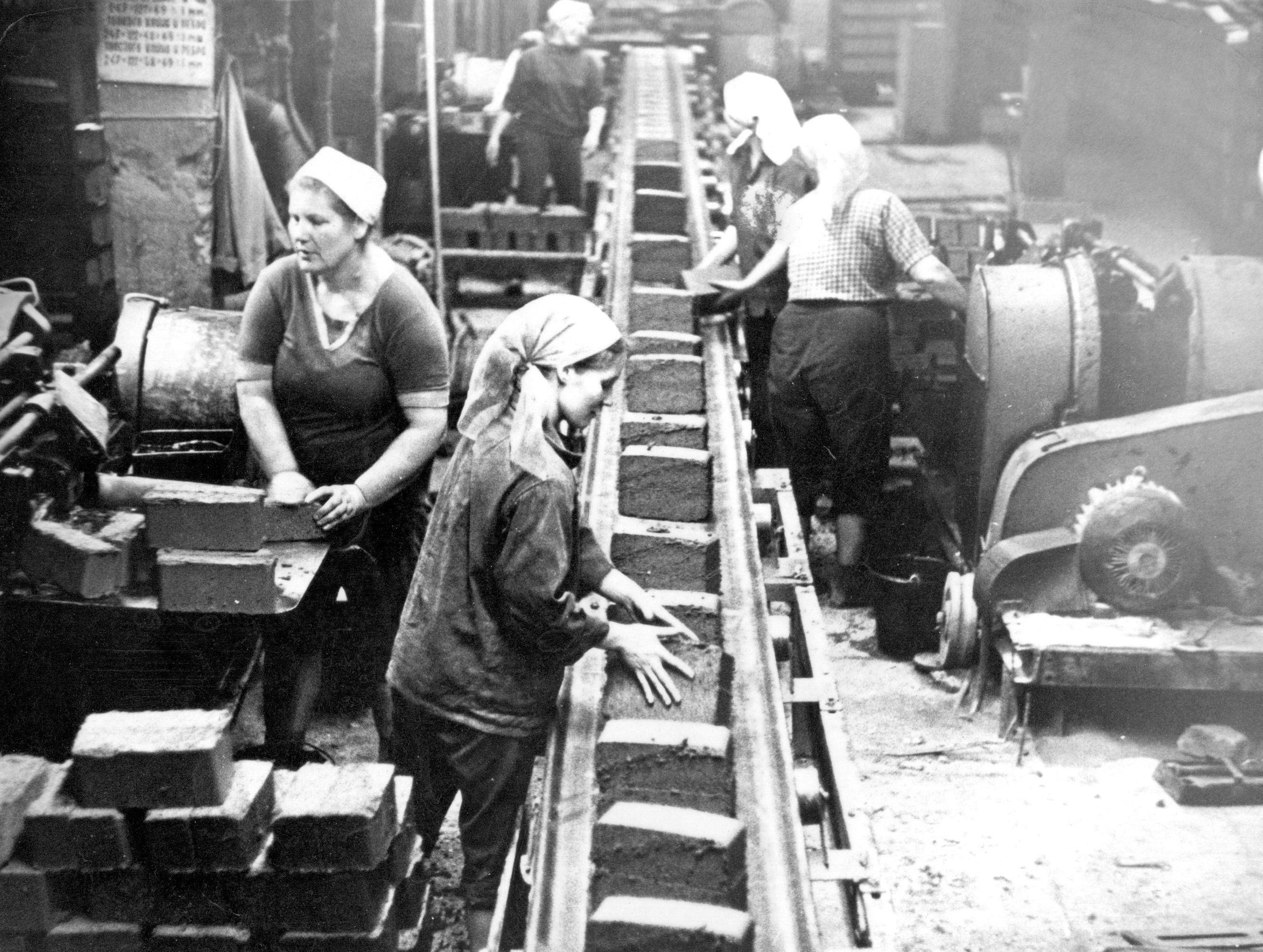
1965-1970
In the mid-60s, an economic reform took place in the USSR, where new planning indicators were introduced: plan of profits, profitability, and return on assets. To move to a new economic reform, production was reoriented towards more profitable products: an increase in the production of bottom cast products, lightweight products, exceptionally complex shapes, and ultra-lightweight products.
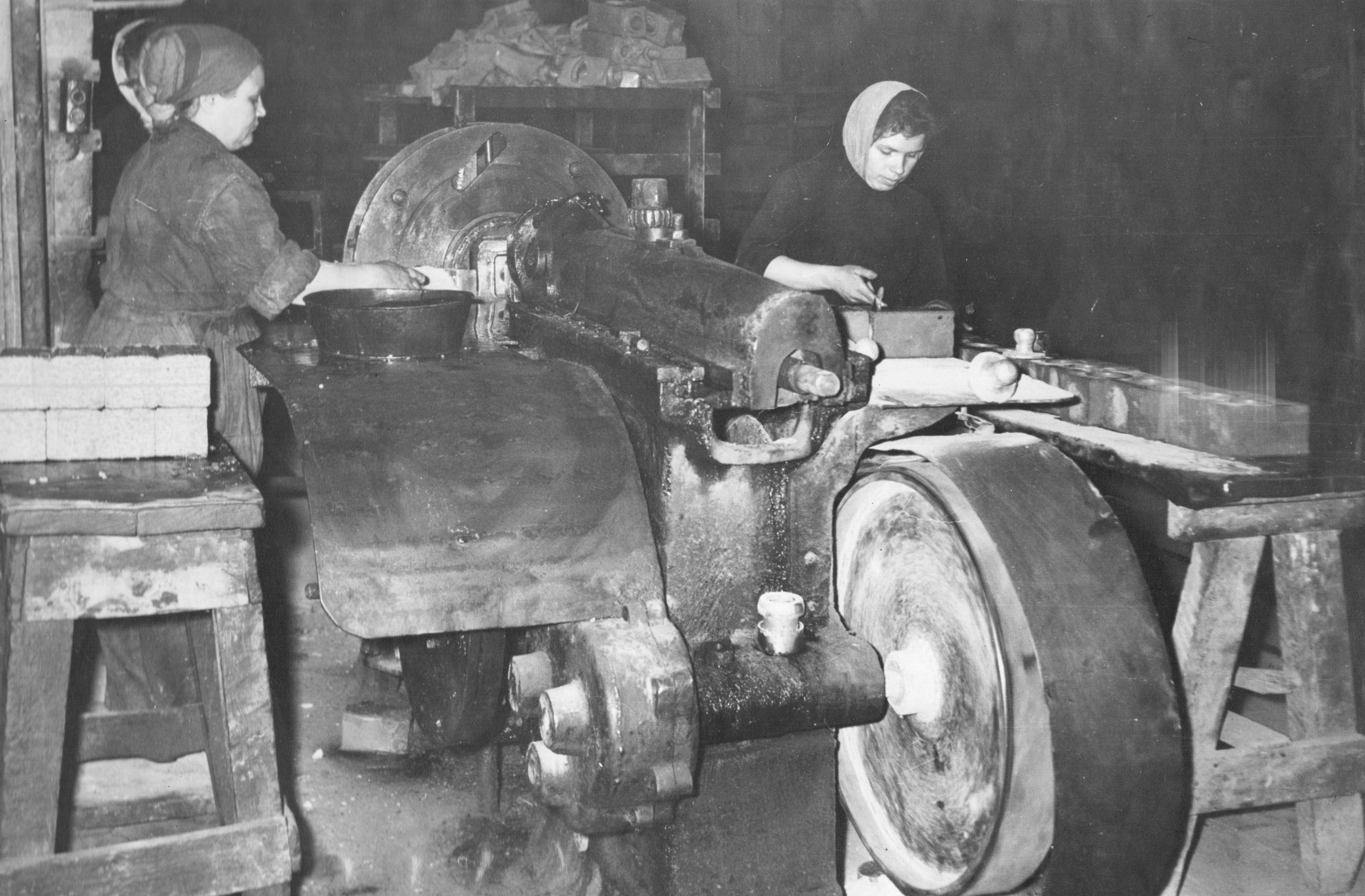
1970
During the eighth five-year plan, universal secondary education for young people was introduced in the USSR. The importance of vocational schools and technical colleges increased. If in 1932 the plant had only one engineer and three technicians, then by 1970 the plant personnel included 17 engineers, 214 technicians, 1,085 highly qualified workers (the total number of personnel at that time amounted to 1,733 people).
By 1970, the Sukhoy Log Fireclay Plant was one of the largest enterprises in the industry with an output of 241.4 thousand tons of refractory products per year.
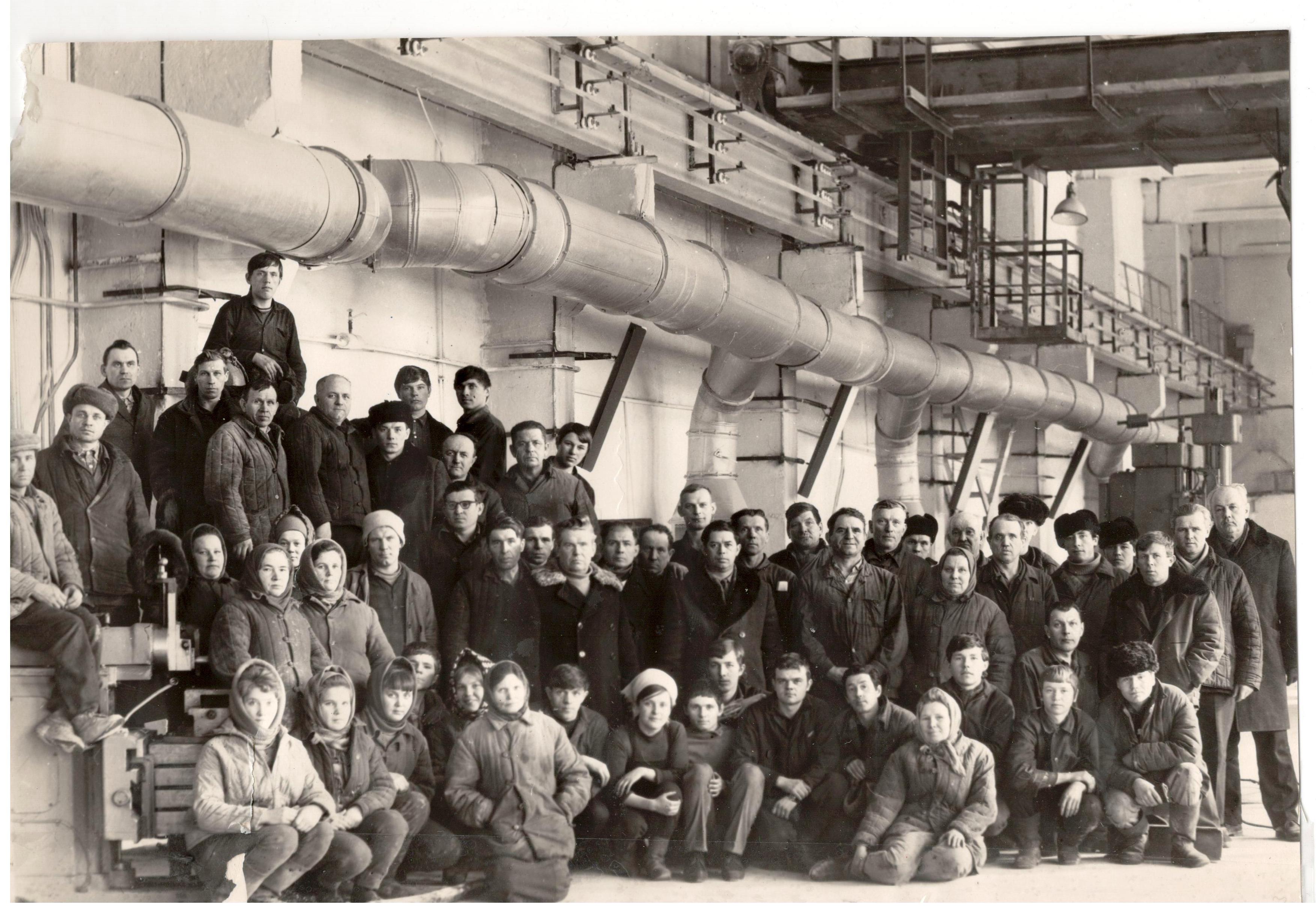
1971-1974
The Sukhoy Log Fireclay Plant was renamed the Sukhoy Log Refractories on February 1, 1971.
A fireclay crushing flow line with an elevator was installed and launched in the grinding shop. Electric vibrators and 25 powerful electromagnets for catching metal were installed on all clay and fireclay flow lines; at the bridge crane site, electric hoists were mounted, four switchboard rooms and a foreman's office were built.
In the gas furnace (calcinating) shop, the modernization of tunnel kilns continued, and a single electric carriage was put into operation for feeding empty stock to the loading area and loaded cars to kilns. In the press and moulding shop, the edge runners were replaced with mechanised ones with automated powder filling. In 1975, the ultra-lightweight shop was brought into service.
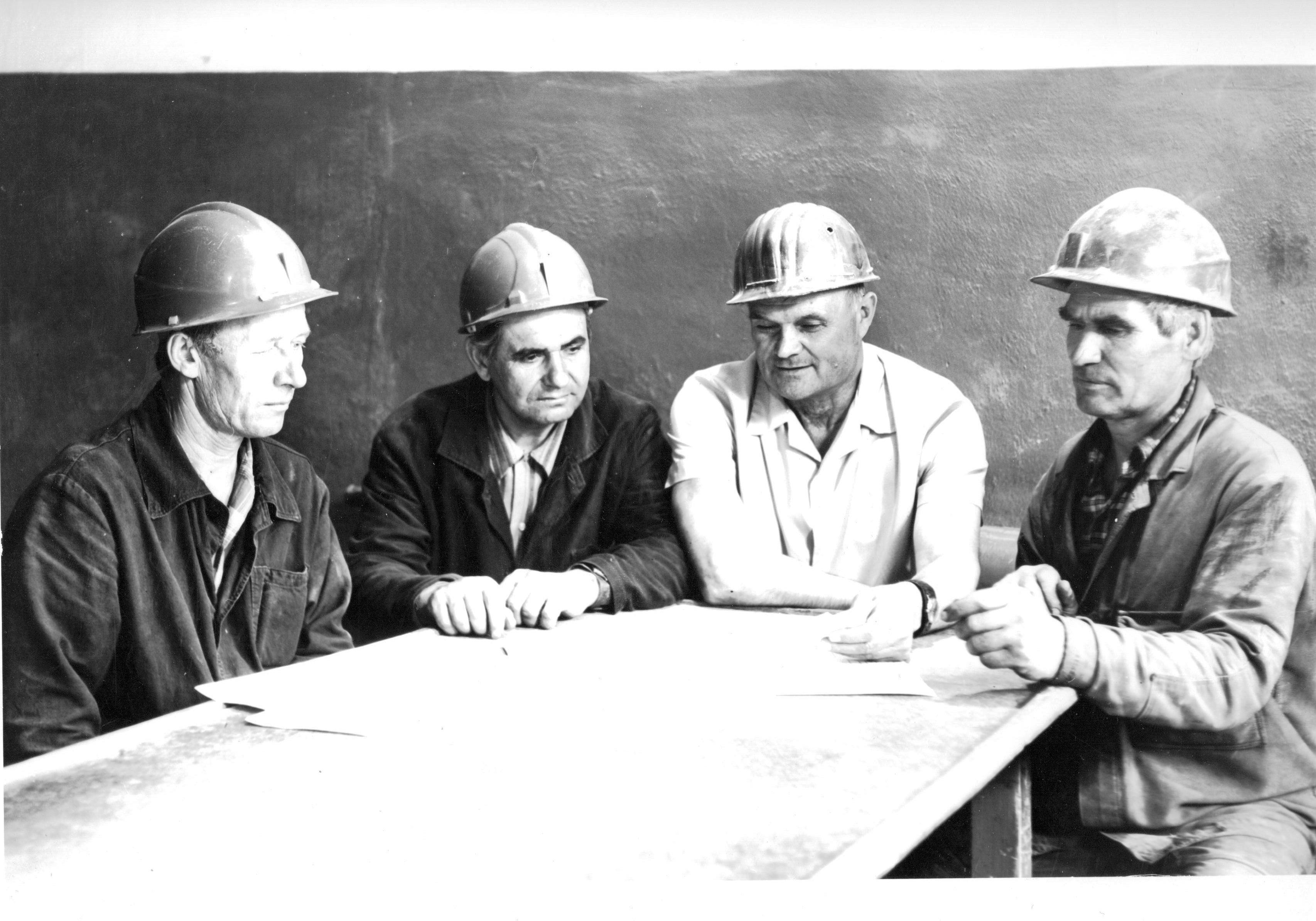
1974-1975
A distinctively effective direction in the plant development and its economy was the arrangement of industrial refractory glass fibre production. The shop was commissioned in January 1974. 1,302 tons of fibrous refractory material were produced, with a design capacity of 1,000 tons per year.
In 1975, due to improvements in production and technology, as well as mastering the continuous process, the design capacity of the furnace No. 1 for fibre production was exceeded. The same year, refractory fibre board production was arranged. These were shipped to the construction of the largest blast furnace in the world at the Krivoy Rog Steel Plant.
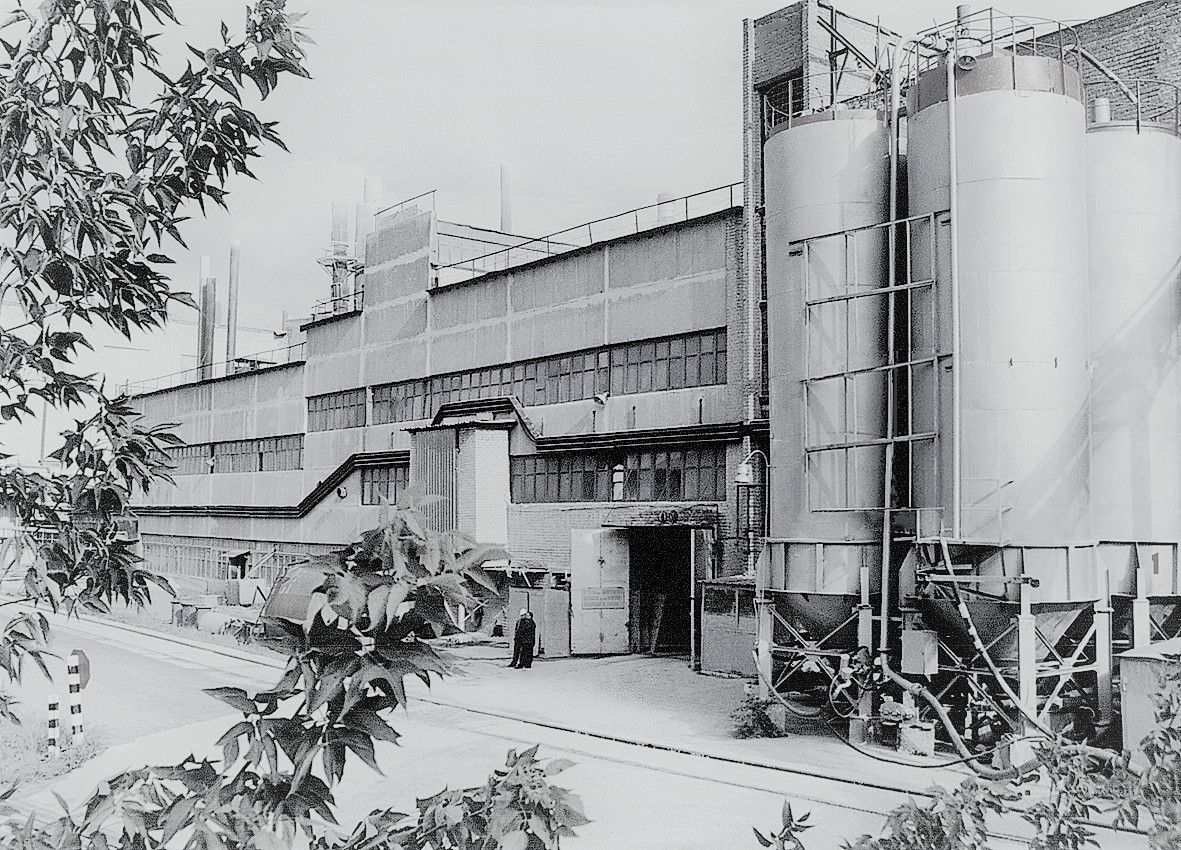
1976-1980
The manufacturing of fibrous materials and products in the glass fibre shop was growing at a swift rate. In 1977, the following amounts were produced: marketable fibre - 1,289 tons, boards - 996 tons, felts - 37 tons. In total, the shop produced 2,322 tons during the year. Mullite silica fibre was awarded the State Quality Mark. In December 1978, the second stage with the SKV-6098 ore-thermal furnace was put into operation.
Mullite silica fibre and related products quickly found their application, as these were in high demand by metallurgical plants and the military industry. Given the high demand for the glass fibre shop products, construction of the third stage was urgently commenced, which was commissioned in the shortest time possible and put into operation in December 1980.
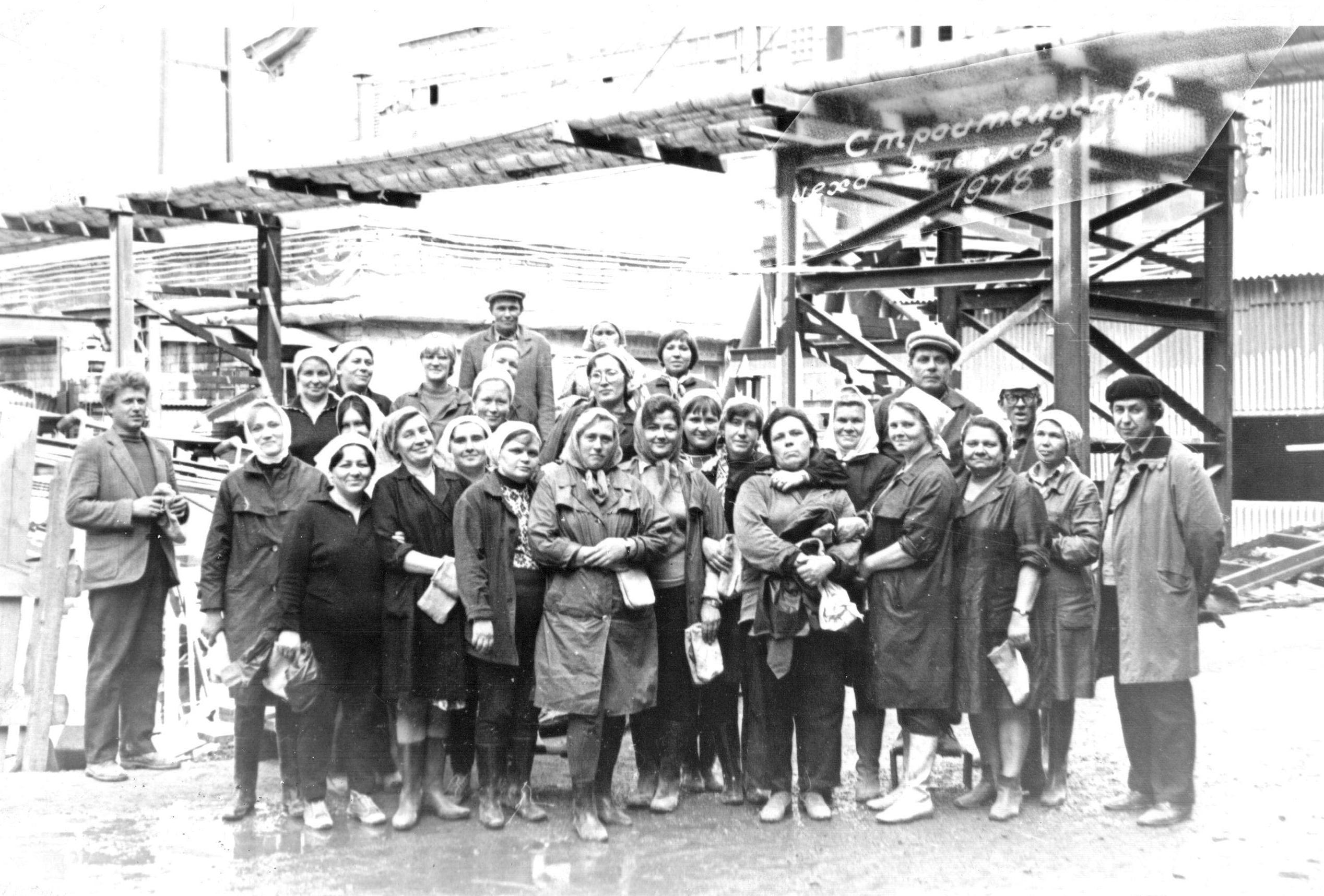
1981-1985
In 1981, a gas system was put into operation complete with a horizontal pumping unit for the calcinating shop and the 5th tunnel kiln. In 1982, the 4th tunnel kiln was converted to natural gas. In the press and moulding shop, the PK-630 were replaced with more efficient ones – SM-1085. A second pneumatic transport line was constructed to feed sawdust from a warehouse and an inclined gallery was installed to feed the mass to the press No. 5.
In the grinding shop, works were performed to convert four drying drums to natural gas, a gallery for feeding fireclay to ball mills and a jaw crusher section were constructed. The fireclay crushing department was put into operation, and the shop for producing lightweight products on a phosphate bond was built.
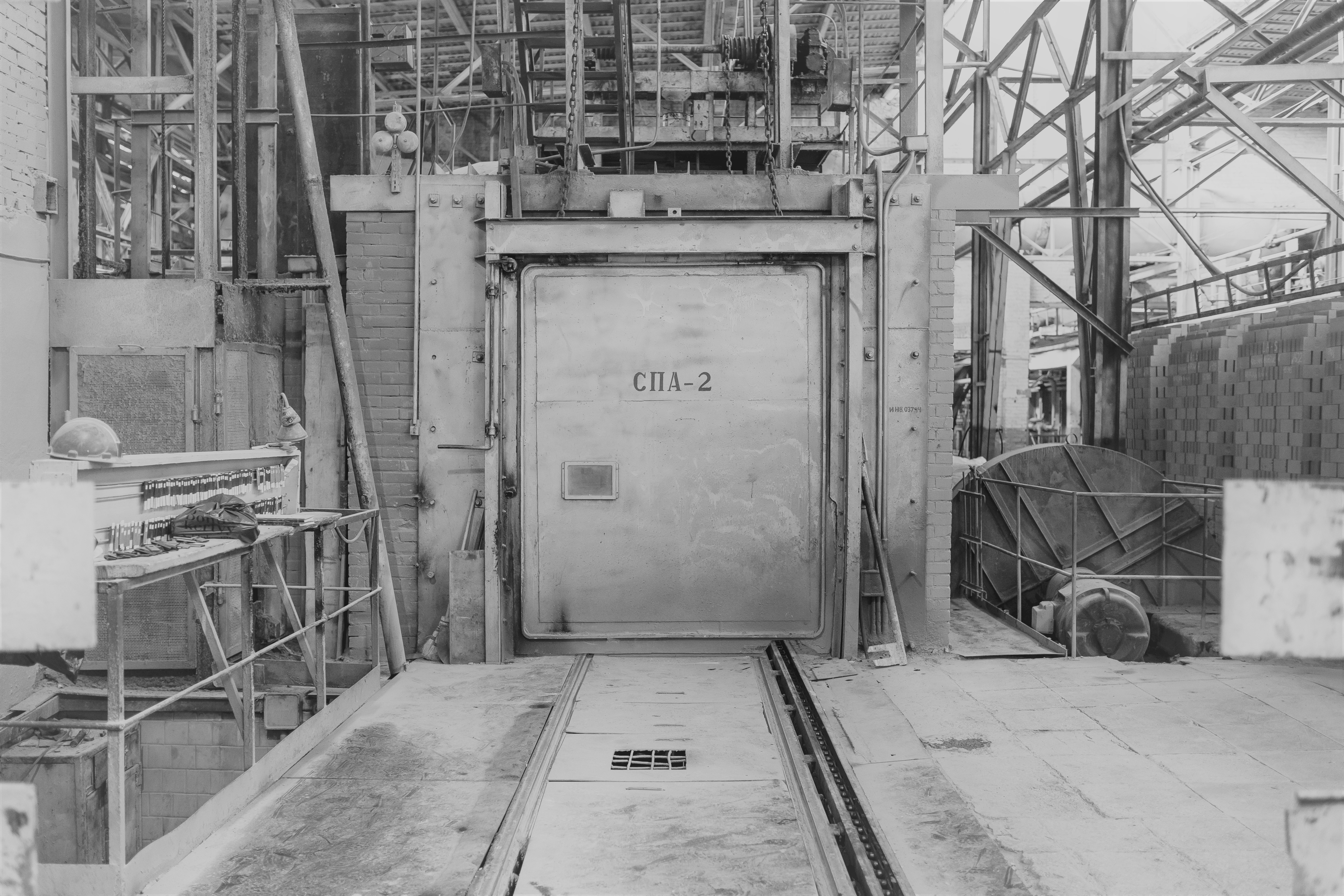
1986-1990
In the ultra-lightweight shop, a tank for receiving alumina through a pneumatic transport system was installed, and a warehouse for storing perlite sand was constructed. In the plastic pressing shop, additional equipment was manufactured and installed for the C-80 and C-88 complex bottom cast grades production.
In the glass fibre shop, under the most challenging conditions, the old electric arc furnaces were dismantled and replaced with new and more efficient dual-jet blast furnaces. Works on technical re-equipment and expansion of the glass fibre shop almost doubled the production of refractory fibre and products based thereon by 1990.
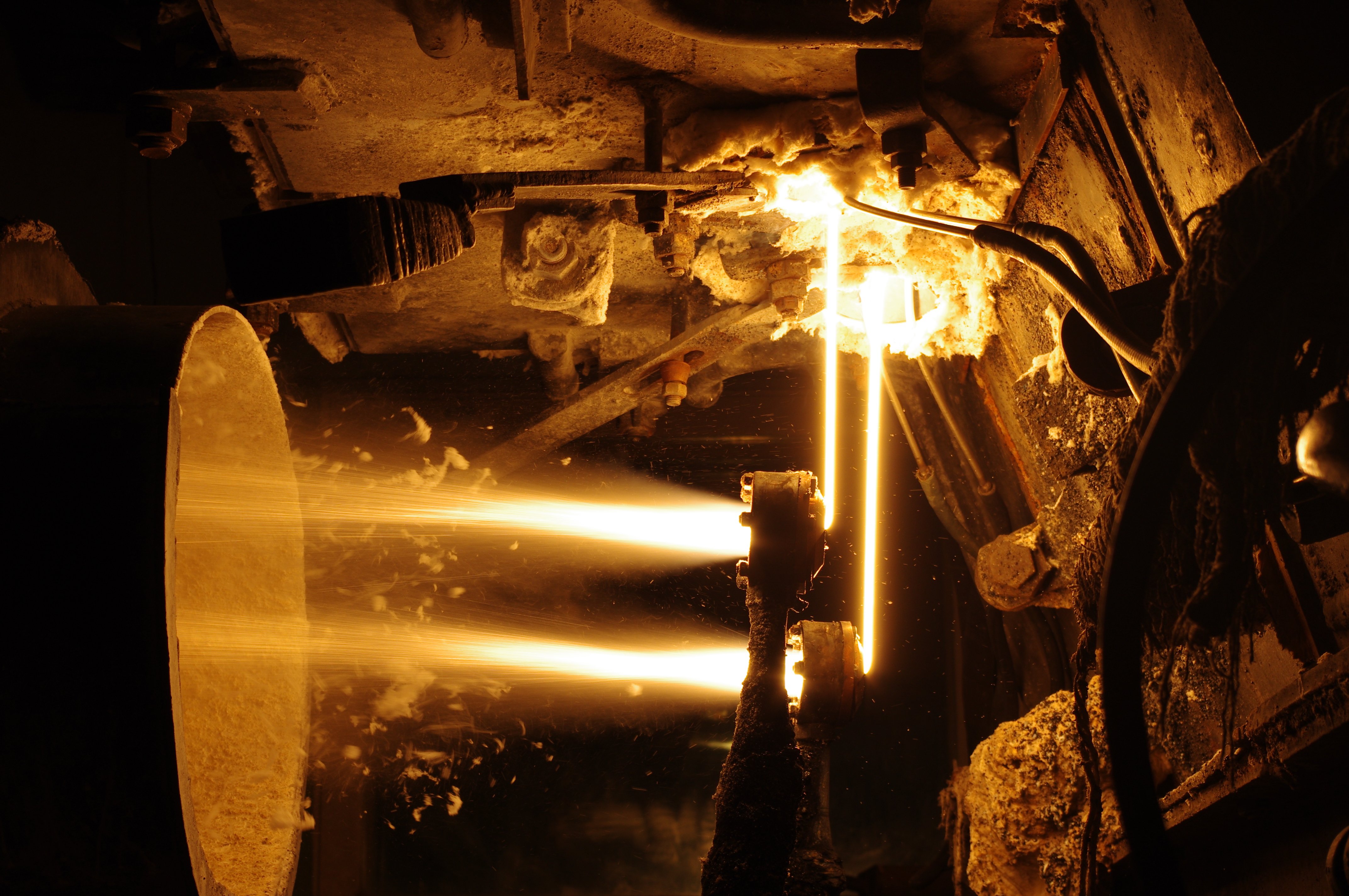
1993
The Sukhoy Log Refractories were transformed into the open joint-stock company on October 25, 1993. By that time, the plant supplied casting pit refractories to 13 metallurgical plants. Lightweight refractory thermal insulators were shipped to 600 enterprises across the country, and 1,500 enterprises received fireclay refractories.
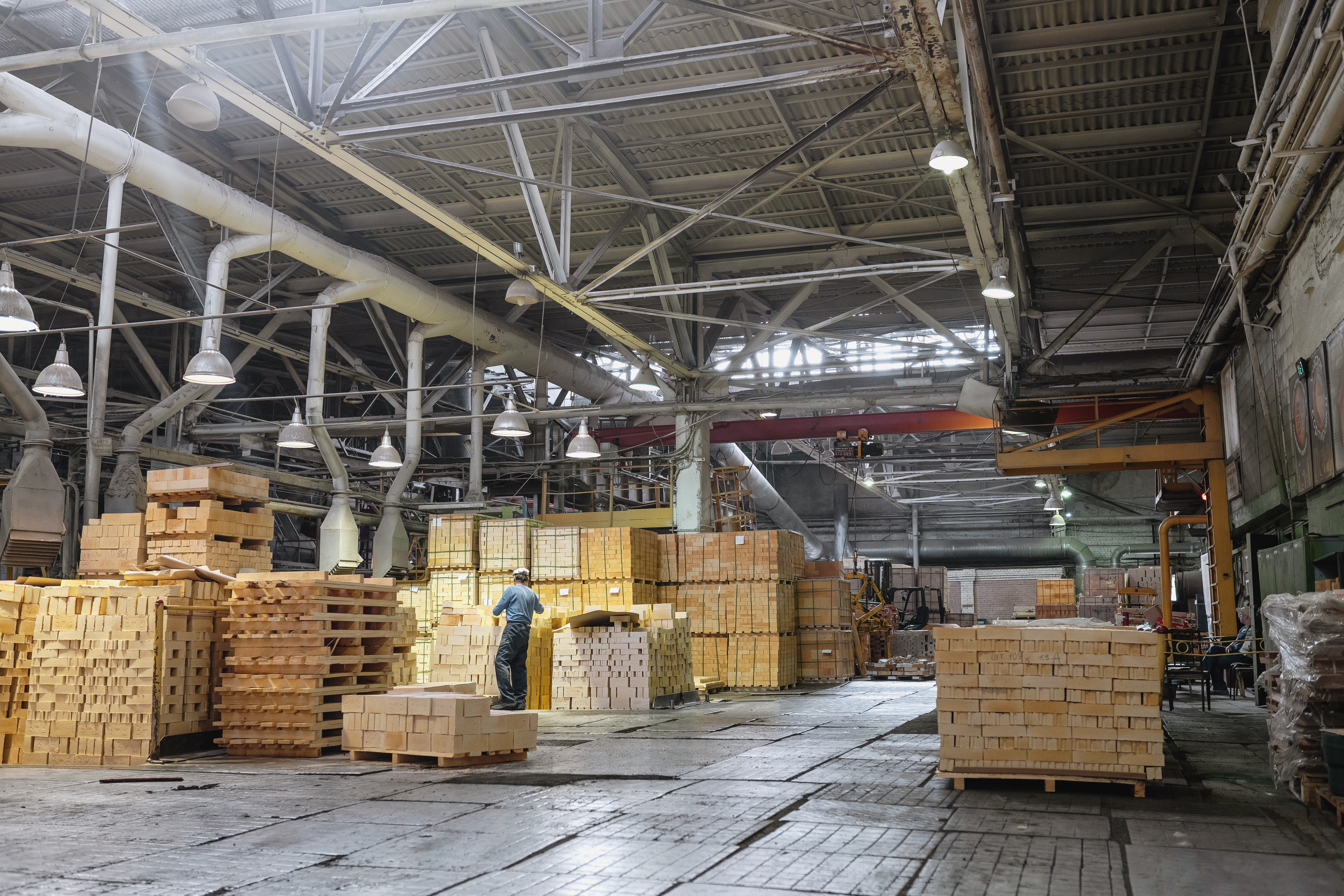
1995-2001
Through this period, the plant’s personnel managed to increase the output of refractory cardboard and complex configuration products made of refractory fibre many-fold due to the technical re-equipment of the products section. A large-scale reconstruction of the grinding shop was completed, which enabled organising large-scale production of unmoulded refractories.
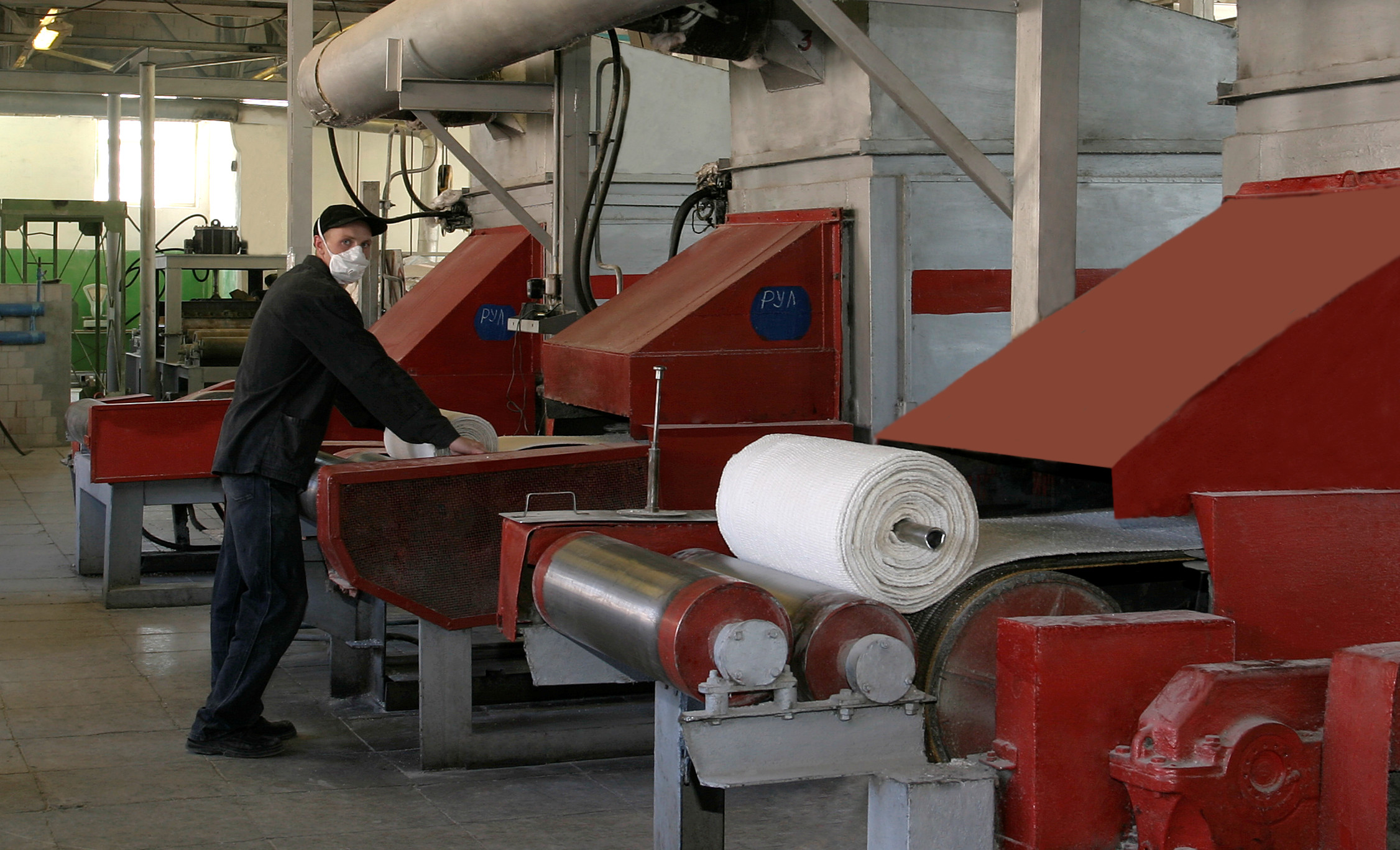
2006
In 2006, on the basis of the Sukhoy Log Refractories OJSC, which was one of the largest manufacturers of fibrous mullite silica materials and products based thereon in Russia, a joint venture, Morgan Thermal Ceramics Sukhoy Log LLC, was established with Thermal Ceramics, the world leader in ceramic fibre thermal insulation production.
A new process line for the production of refractory ceramic mullite silica glass fibre using the centrifugal method was installed and commissioned. The estimated line capacity is 3,500 tons/year.
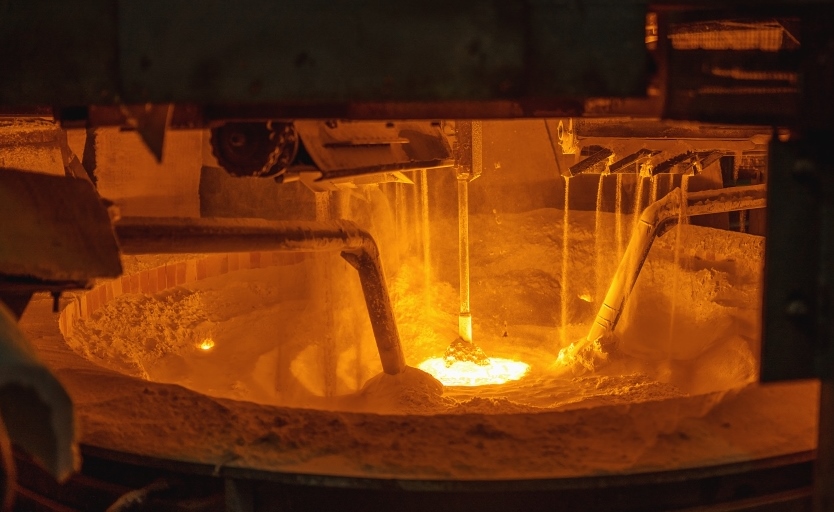
2009
The technology for producing refractory ceramic glass fibre was elaborated. The line was officially launched in May of the following year. The line for producing rolled materials was designed and built with a high level of automation of all processes, from charge preparation to cutting of finished material.
All stages were subject to video and electronic monitoring with 400 parameters recorded on a computer every 20 minutes. A high degree of process automation enabled obtaining materials with specified parameters that fully complied with the global quality standard of Thermal Ceramics.
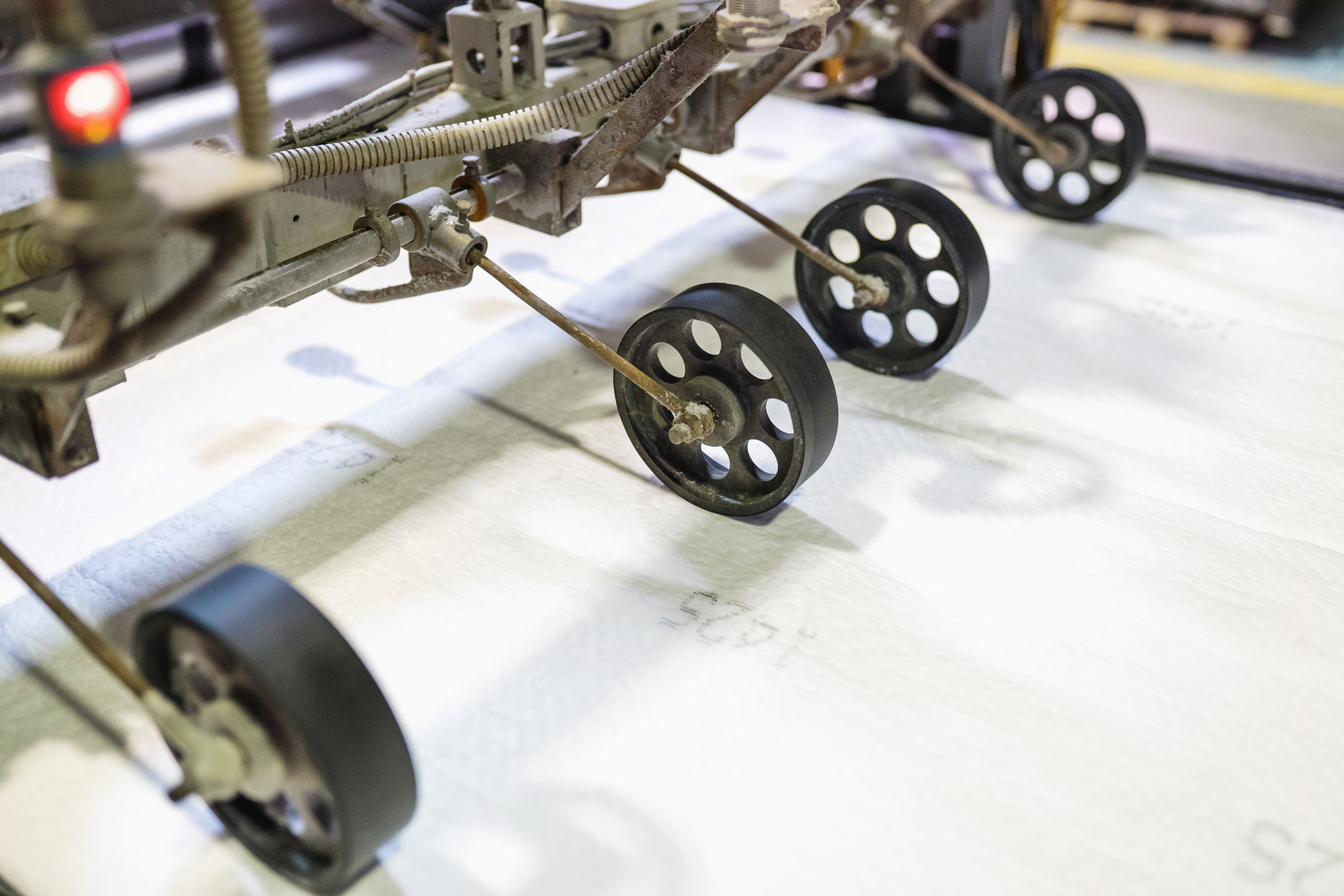
2011
In the first half of 2011, installation works were completed and the technology for producing vacuum-formed, large-format thermal insulation boards as per Thermal Ceramics technology was elaborated.
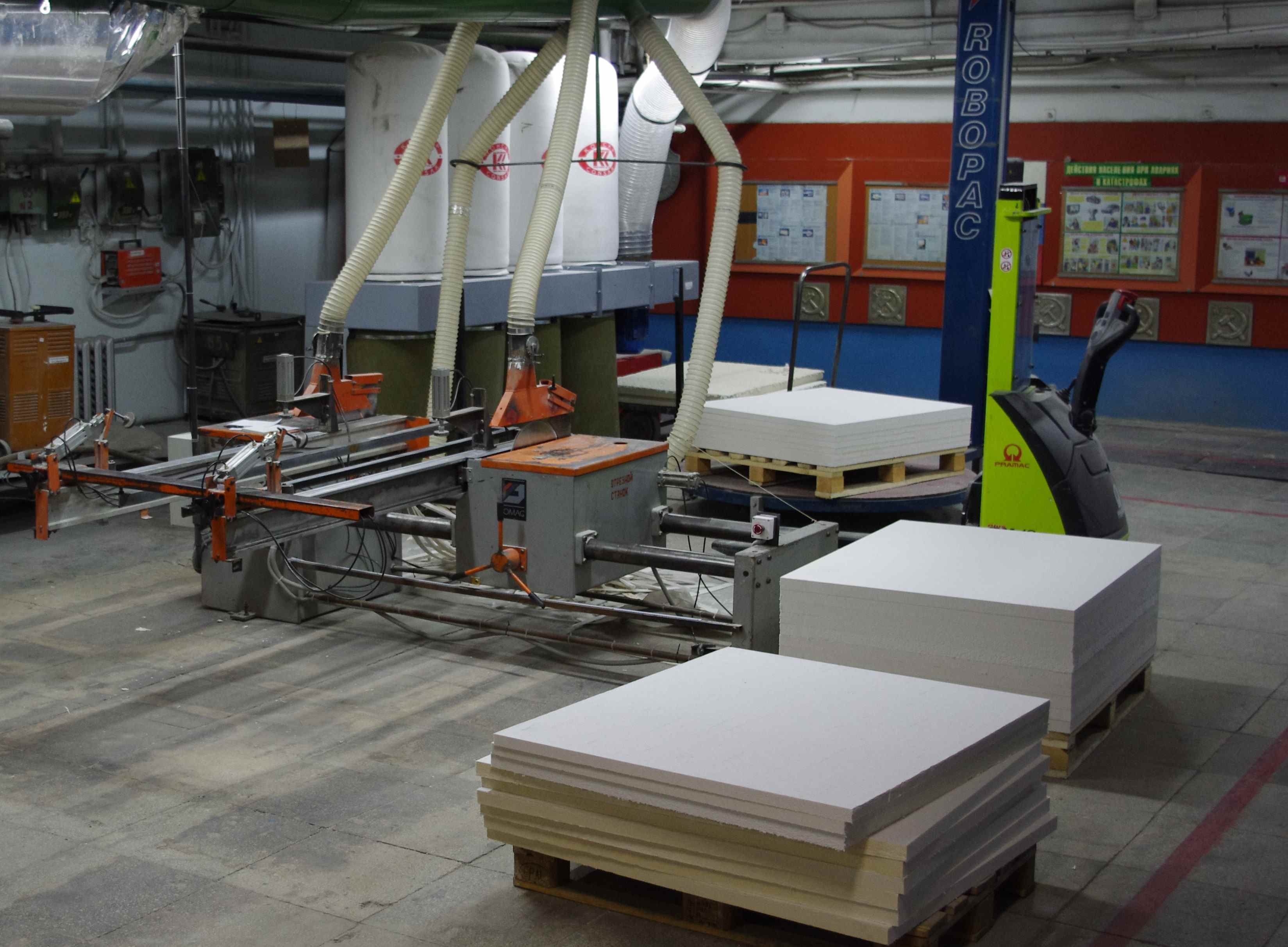
2013-2014
In 2013, the Sukhoy Log Refractories acquired one of the leading Italian companies producing thermal insulation products and unmoulded refractories - NUOVA ISOLTERMICA. By 2014, all production lines were moved to Russia.
The technology for producing a completely new grade of thermal insulation products called SL was elaborated. SL 23, SL 26, SL 28, SL 30 products comply with the ASTM international standard and can be used in thermal insulation layers of linings made according to the designs of leading international engineering companies.
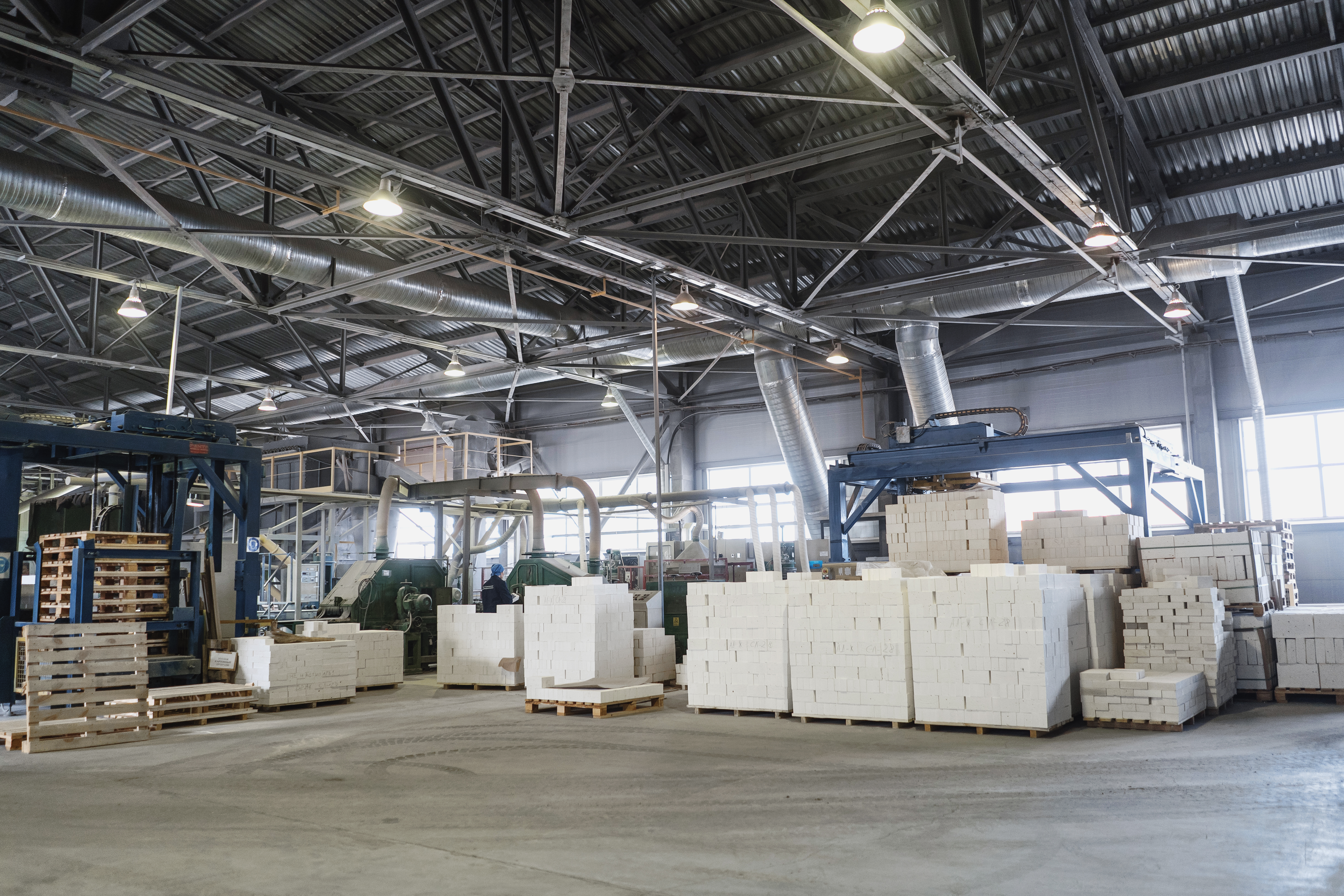
2015
A new tunnel type furnace N1 of the molding and calcination bay was put into operation on 1 June 2015. Sukhoy Log Refractories OJSC launched the industrial production of moulded high-alumina and corundum refractory and thermal insulation products.
The production of unmoulded refractories and dry refractory concrete mixtures was scaled up drastically.
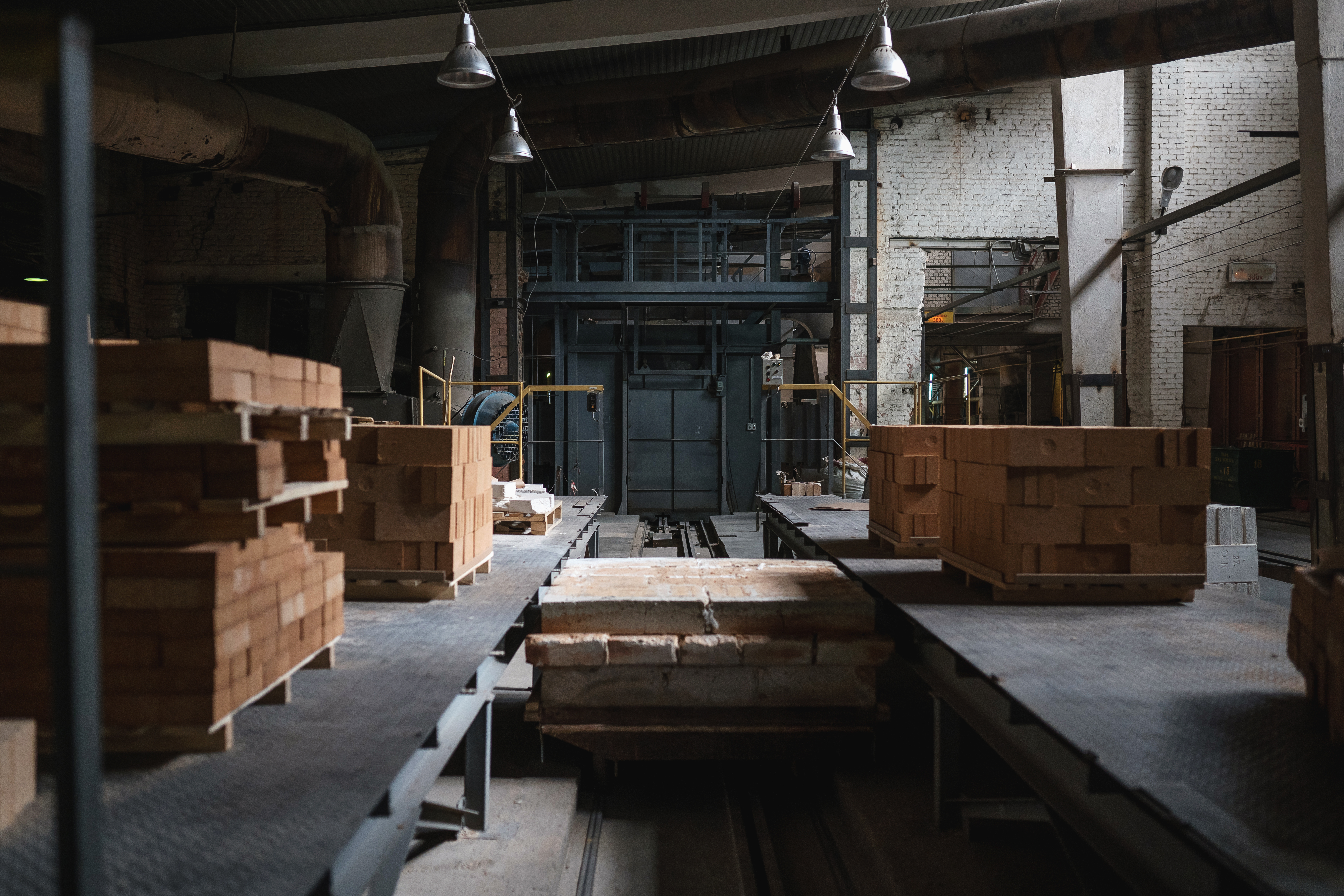
2016-2020
The range of moulded dense refractories produced was significantly expanded. The following grades, completely new for the enterprise, were mastered: MKRS-45, MKRU-45, MKRP-45; MLS-62, MKS-72, MKU-80; MKS-90, KP-95, KS-95, KU-95; packed products for air heaters of ShV-37, ShN-38, ShV-42, and MKRN-45 grades.
The range of thermal insulation refractory products was expanded. In addition to the plant’s traditional products of the ShT (from ultra-lightweight 0.4 to 1.3) and MKRT (0.7-0.8) grades, a significant share of the manufactured products was made up of MLT-1.3 grade products. In addition, upon successfully elaborating the technology in laboratory conditions, the enterprise was preparing to produce a pilot batch of corundum thermal insulation products of the KT-1.1 and KT-1.3 grades.
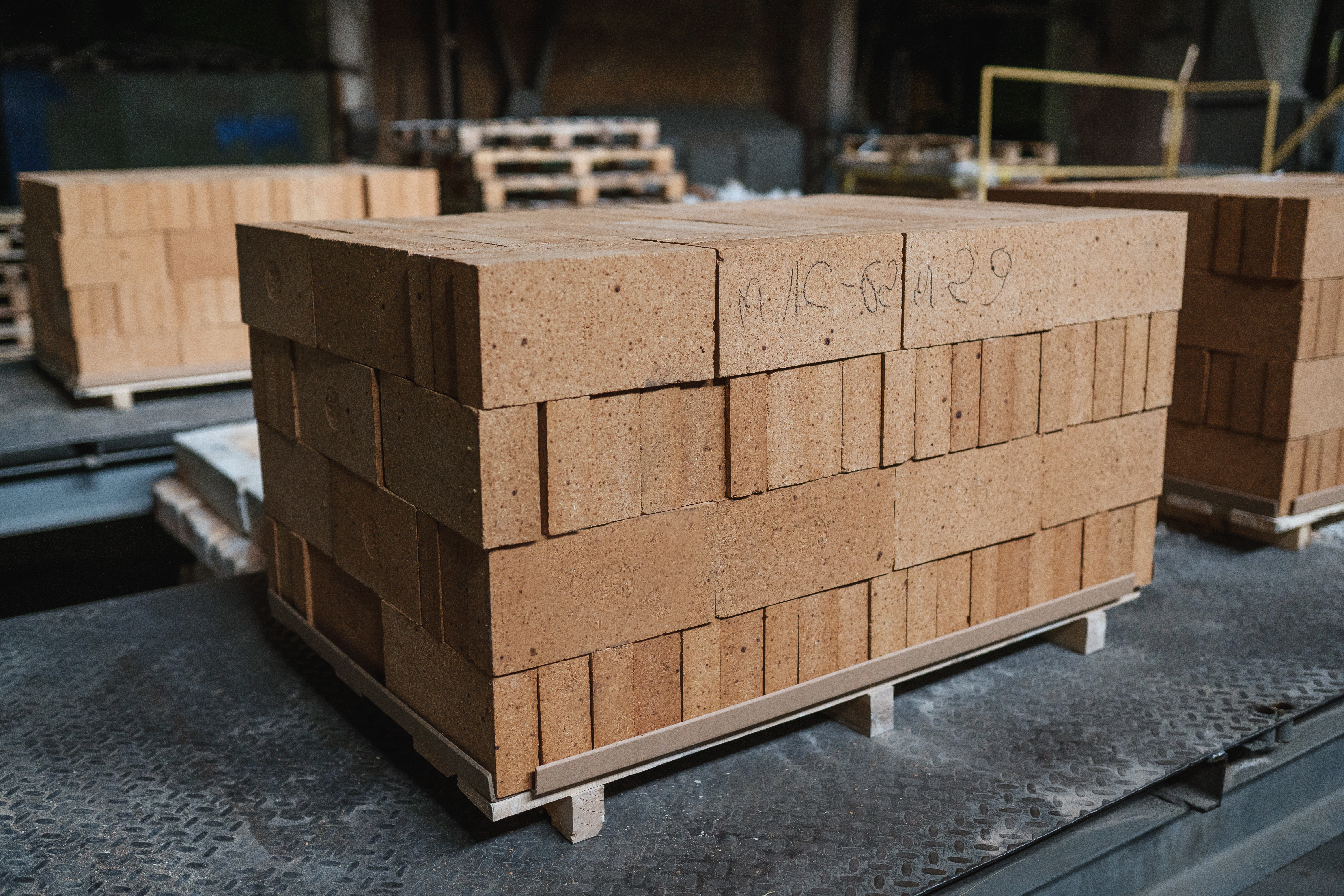
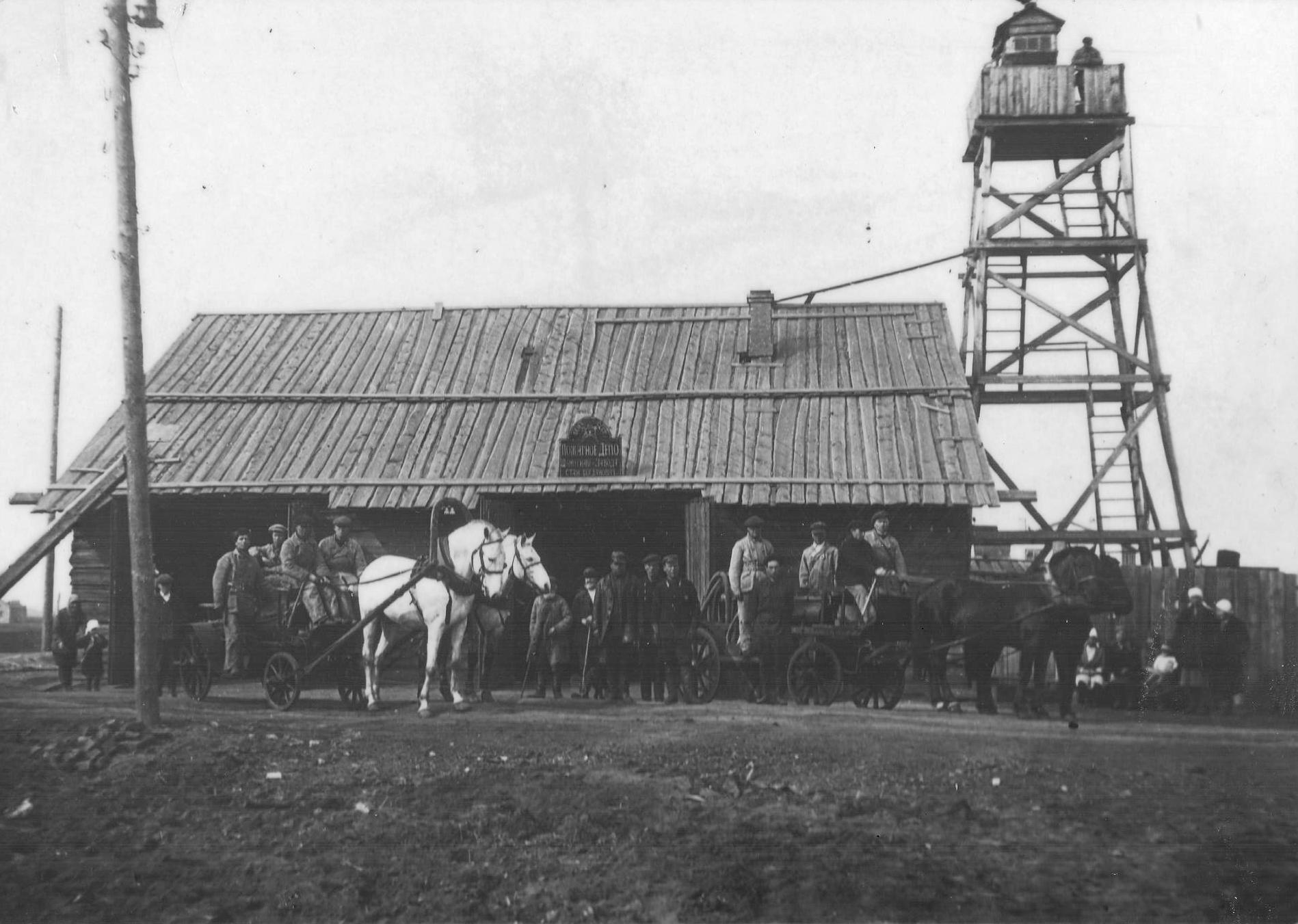
1928
In the 1920s, the USSR embarked on industrialization. The gigantic construction that was underway in the country required large volumes of building materials. In 1928, construction of the Sukhoy Log Integrated Plant began in the Ural (now Sverdlovsk) Region, which included cement, fireclay, slate, lime plants, and the Belaya Glina mine.
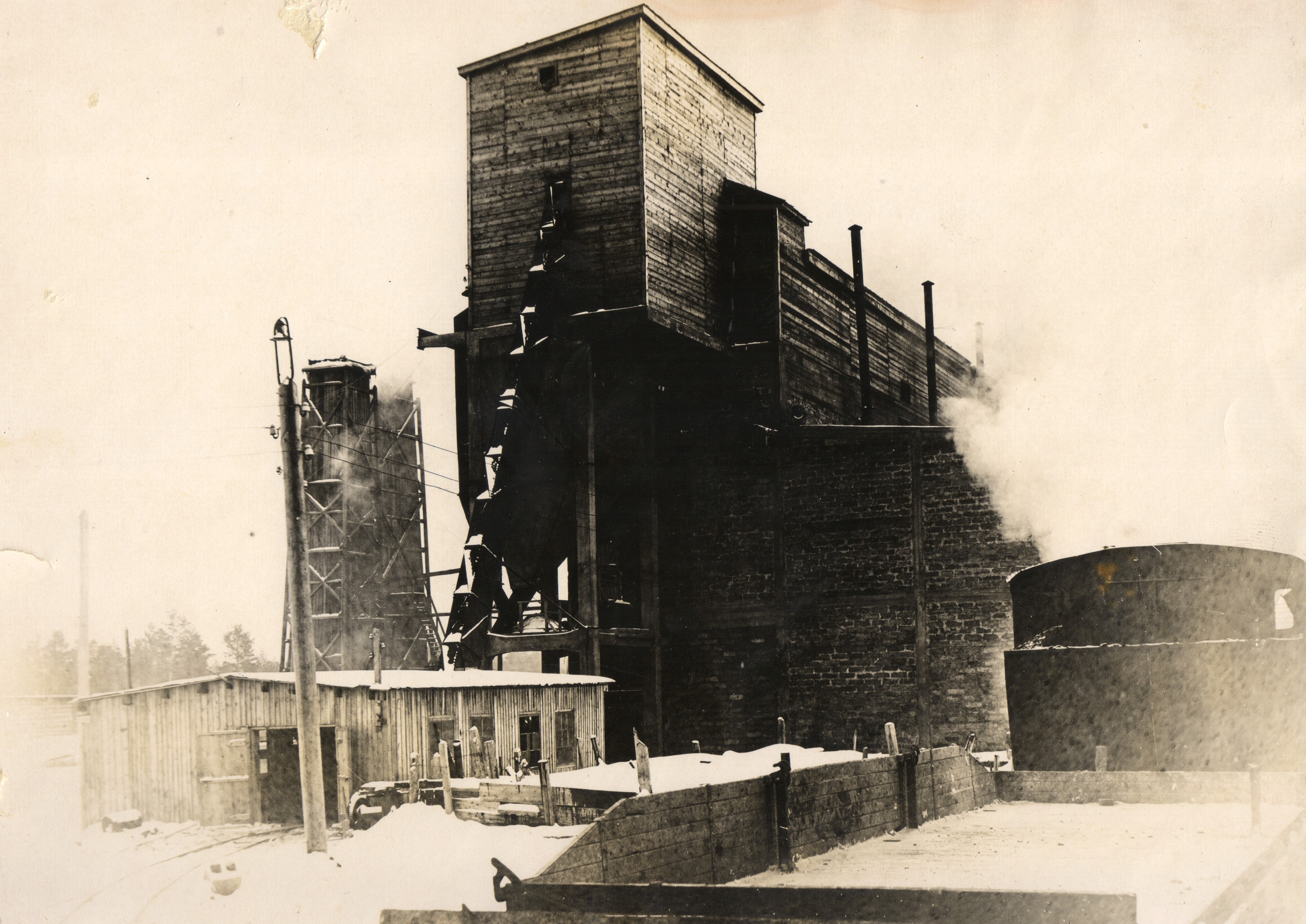
1930
In 1930, construction of the Sukhoy Log Fireclay Plant commenced. According to the Central Archives of the National Economy of the USSR, the Sukhoy Log Fireclay Plant was constructed among the first 37 enterprises in the Urals subject to mandatory commissioning in the first five-year plan, so the plant was erected ahead of schedule in order to provide refractories to the heavy industry enterprises being built.
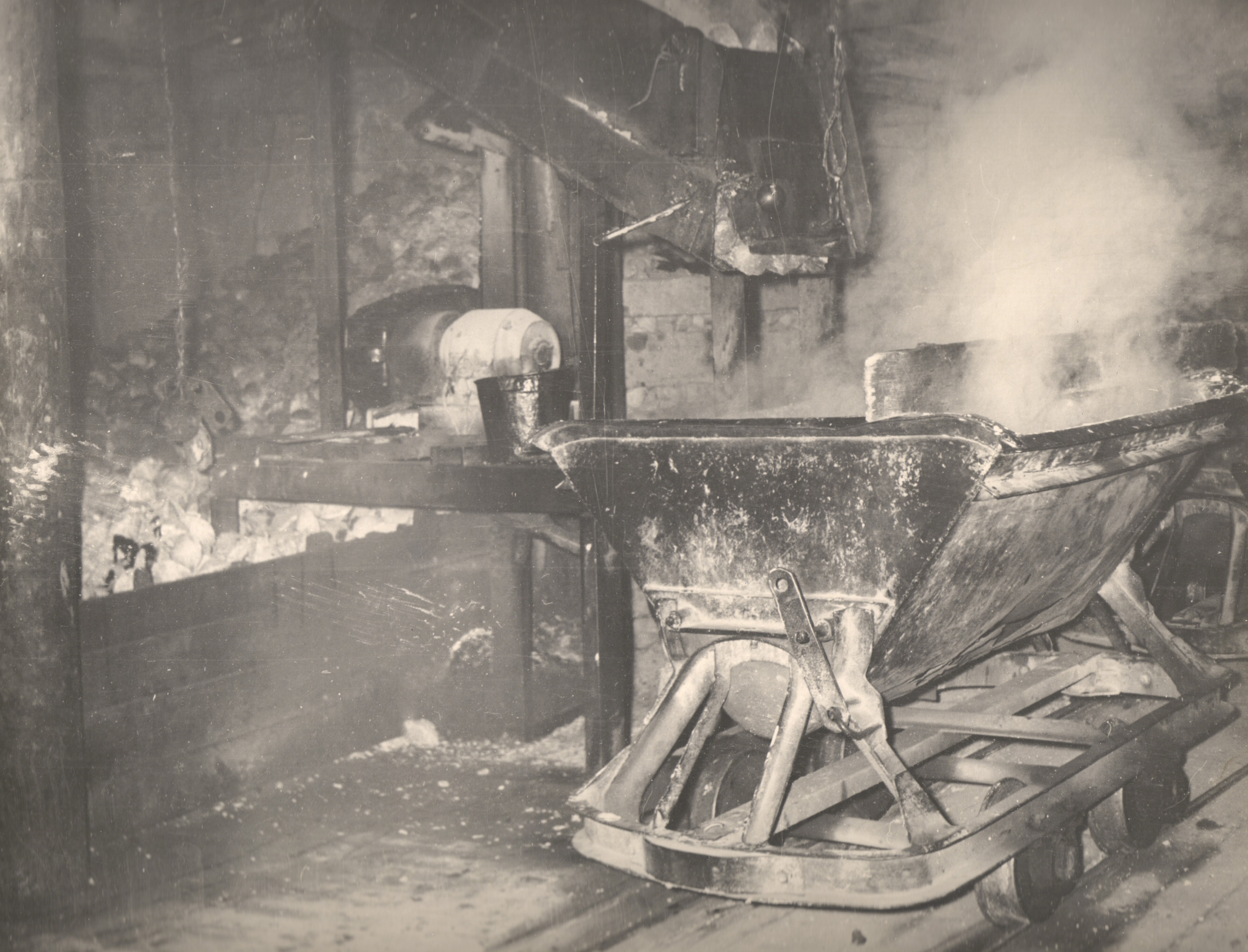
1931
Concurrently with the construction works, equipment installation was performed. The fireclay plant equipment was supplied from Germany, so the installation was carried out under the supervision of German experts. The following units were constructed: Khirta No. 1 tunnel kiln, ball mill No. 1, drying drum No. 1, auger extruder No. 1 with Ruchaud presses No. 1-2, 19-way dryers and chambers, shaft kilns designed by engineer Gross, gas generator station.
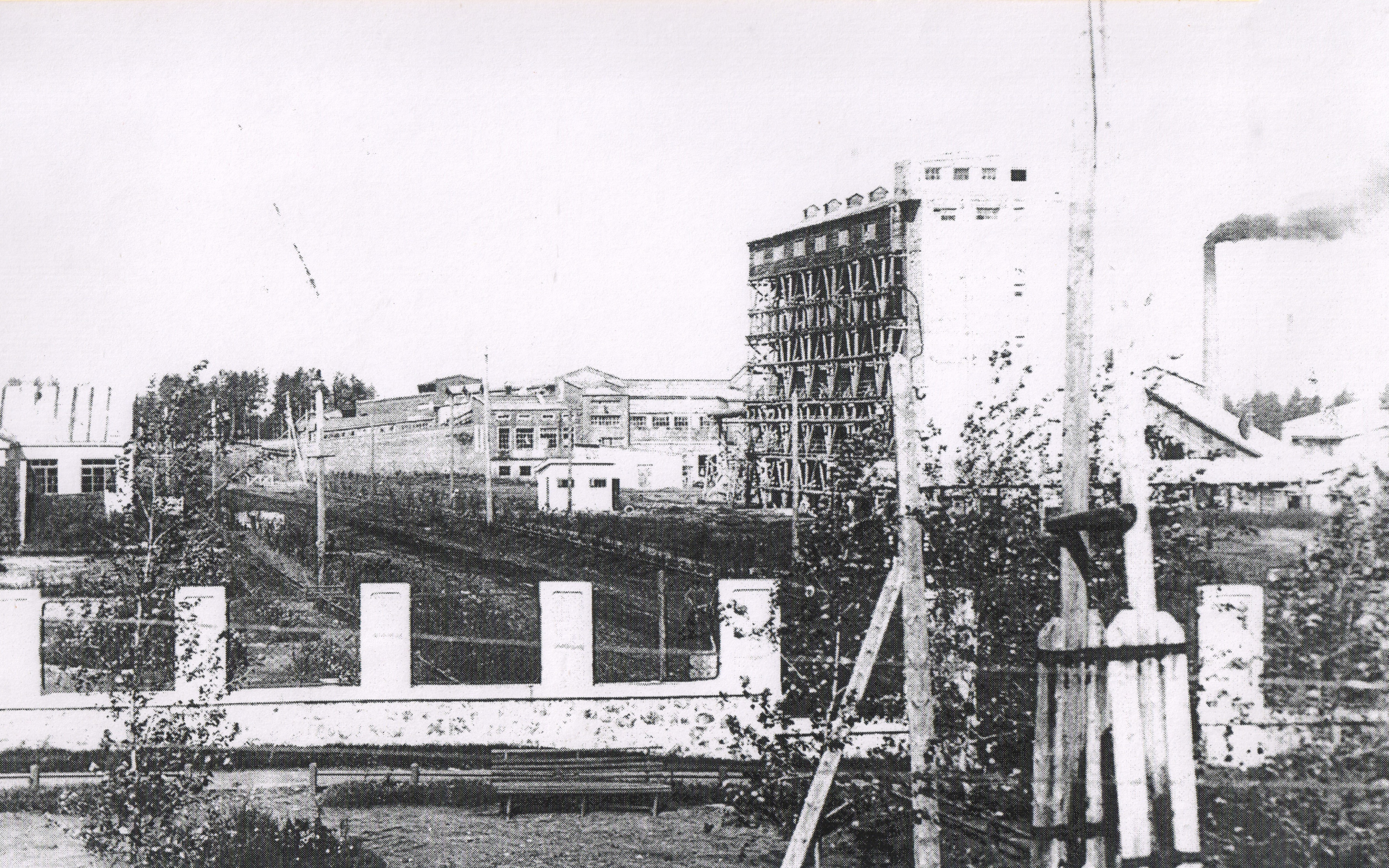
1932
On March 27, 1932, the first plant in the Urals and the east of the country producing fireclay refractory products was put into operation. By the late 1932, 6,752 tons of refractory products were produced, including 234 tons of ordinary shapes. For the first three years, the plant produced only fireclay products, and in the fourth year, the production of casting pit refractories for bottom casting was mastered.
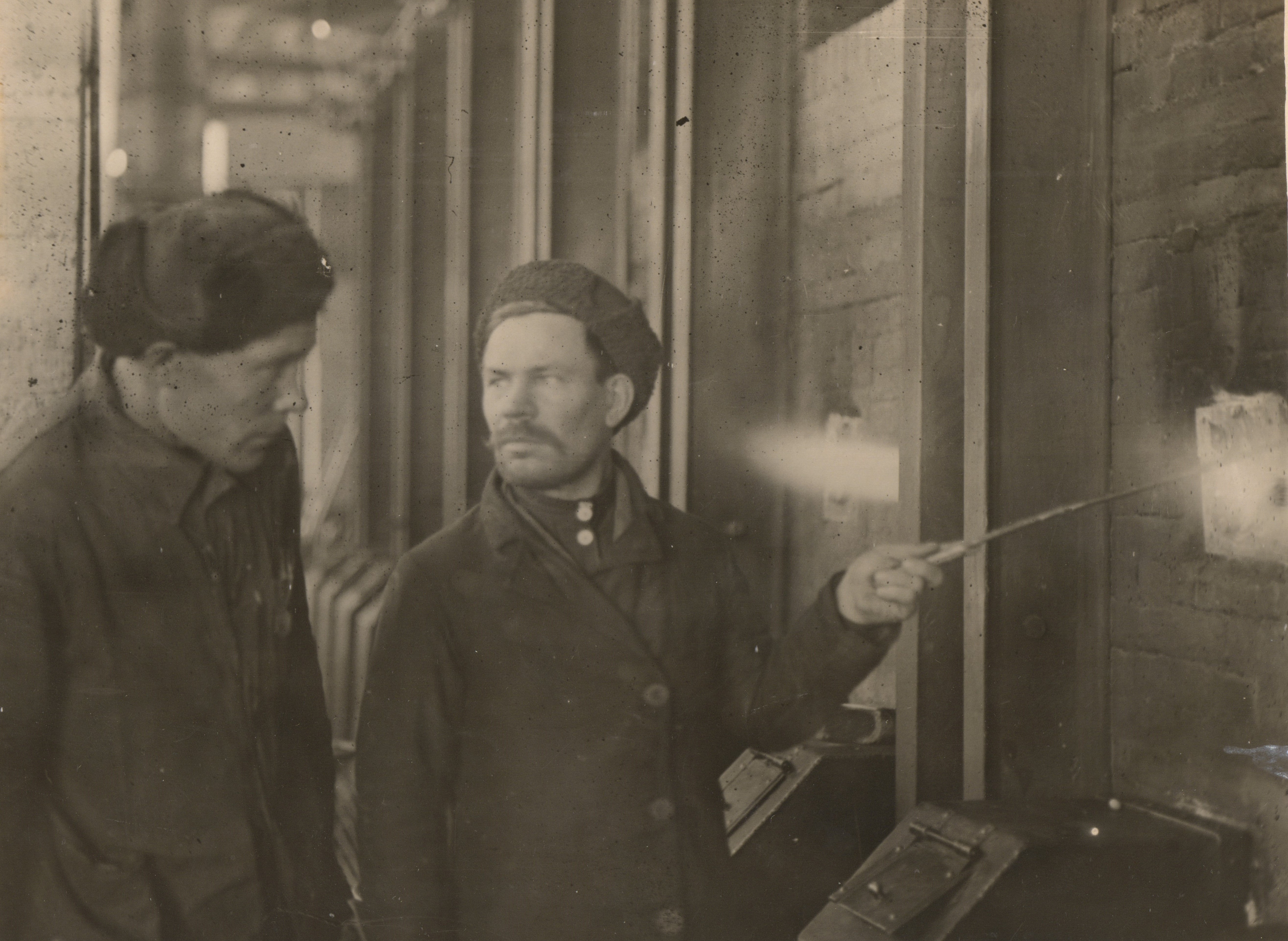
1933-1934
In 1933, the plant was already operating at full capacity. 14.6 thousand tons of refractories were produced. In 1934, the 2nd Khirta tunnel kiln was put into operation. Due to its launch, the volume of refractory production increased to 26 thousand tons per year. The plant utilized German equipment: Raupach and Ruchaud presses, as well as Berper crushers.
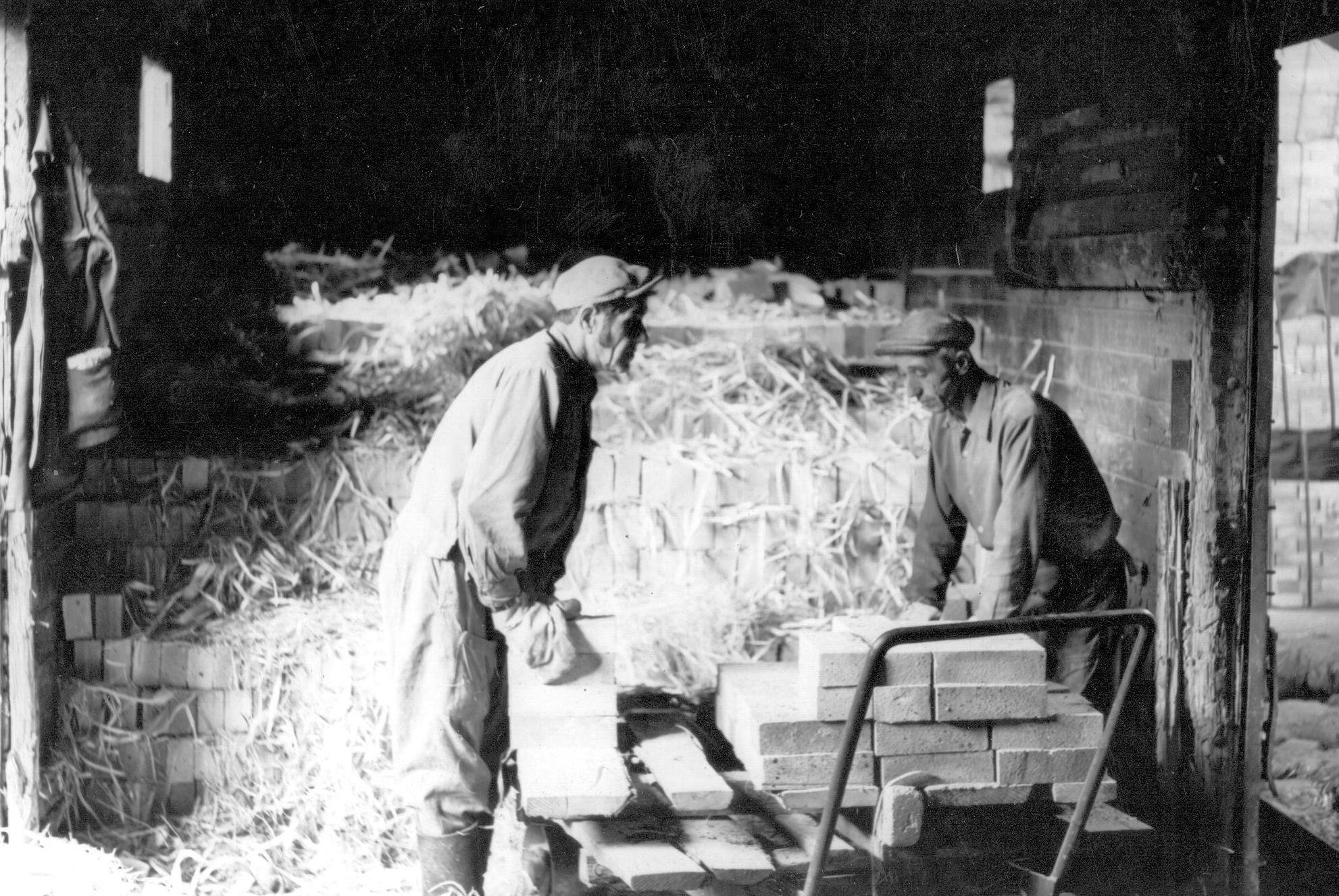
1935-1940
In 1935, 3 thousand tons of Cowper bricks for blast furnace air heaters were shipped to the Magnitogorsk Iron and Steel Works (aka Magnitka) alone. In 1940, the second line of the moulding shop was built and put into operation; production output reached 51.9 thousand tons of refractories, the increment in output compared to 1938 was 31.0%.
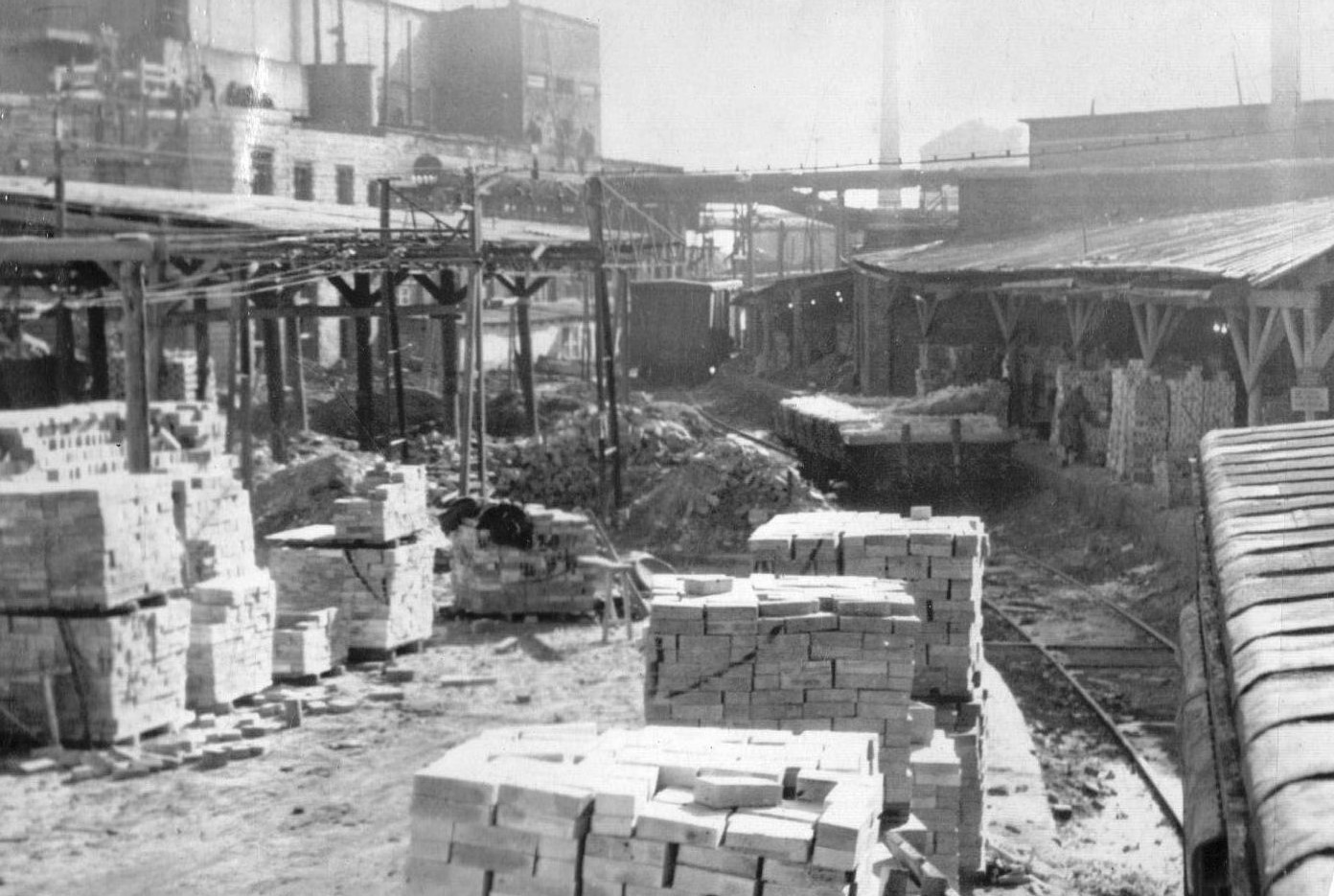
1941-1943
Over the harsh years of the Great Patriotic War, when many of the country's refractory enterprises found themselves in territories temporarily occupied by the enemy, the plant's personnel had to solve the problems of mastering and increasing the production of many complex types of refractory products within the shortest time possible. The plant construction went on: drying drum No. 2 and ball mill No. 2 in the grinding shop, as well as two annular furnaces in the furnace shop were put into operation.
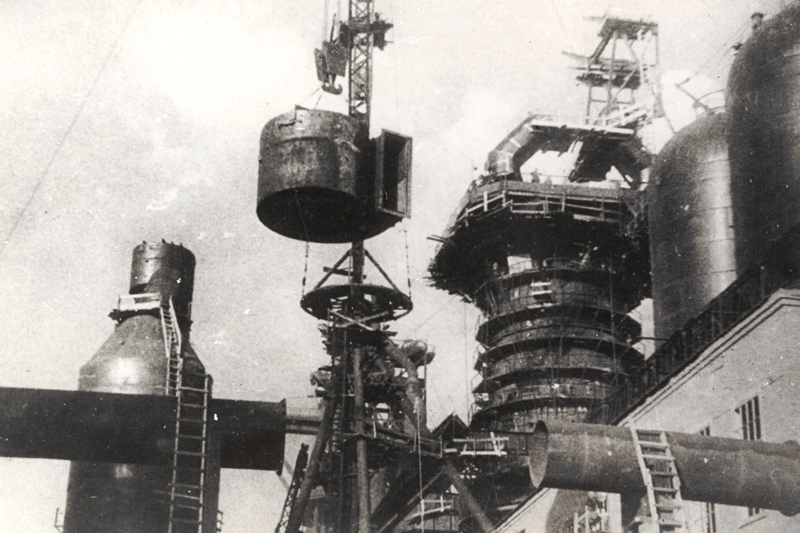
1943-1945
On the orders of the State Defense Committee, in 1943 the plant personnel quickly set up mass production of refractories for the construction of the sixth blast furnace at Magnitka. Trains with hot air bricks were sent out days and nights right on time. All plant workers took part in loading the refractories. On December 23, 1943, Magnitka's sixth blast furnace produced its first cast iron.
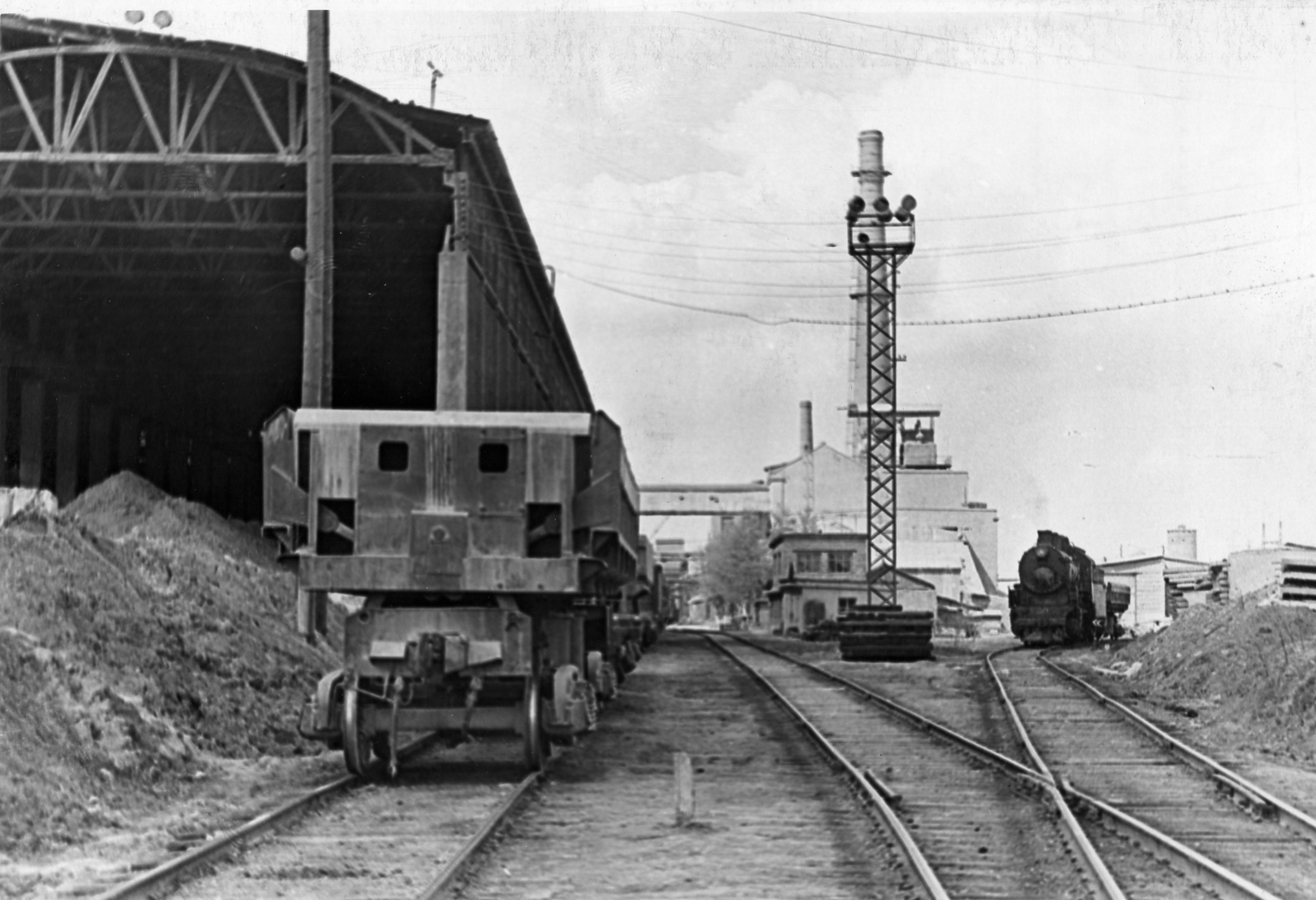
1946-1950
The plant equipment capability increased from year to year. In 1947-1949, drying drum No. 3 and ball mill No. 3, as well as clay and fireclay flow line No. 2 were put into operation in the grinding shop. The Sukhoy Log refractory men successfully fulfilled the production plan by the end of the fourth five-year plan (the number of personnel during those years was 1,360 people). The country's metallurgical industry received 429.8 thousand tons of refractory products.
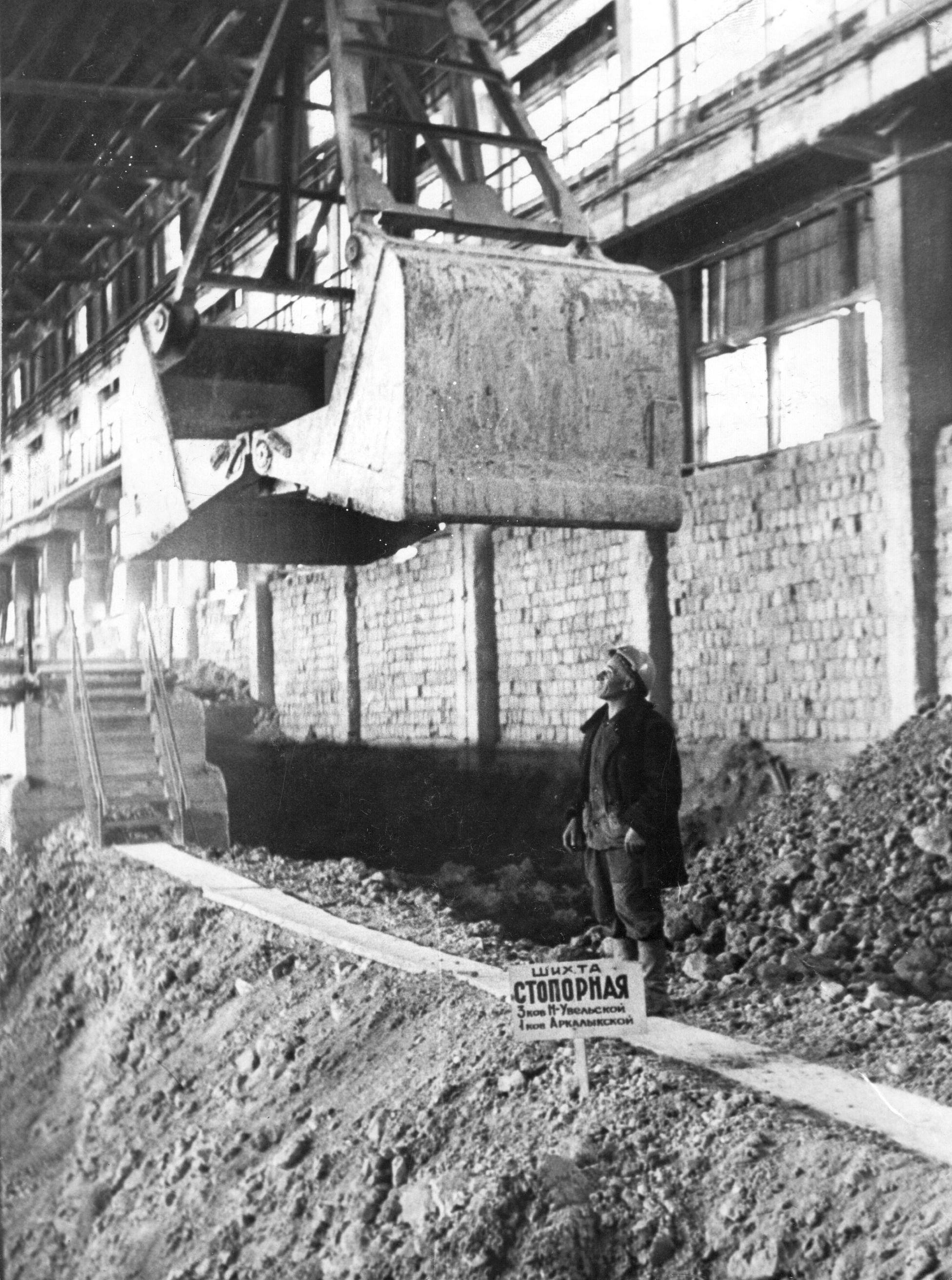
1951-1955
For the fifth five-year plan, the fireclay plant personnel tasks were closely connected with the construction of large metallurgical enterprises in the USSR. Significant expansion of refractory production lied ahead. Addressing these issues required the introduction of additional production areas, reconstruction of old ones, mastering new processes, and introducing advanced equipment.
The personnel managed to complete the fifth five-year plan and the tasks set for production development. The country's metallurgists received 718.6 thousand tons of refractories. The production output in 1955 increased by 175% compared to 1951, and by 167%, or 289 thousand tons, compared to the results of the previous five-year plan.
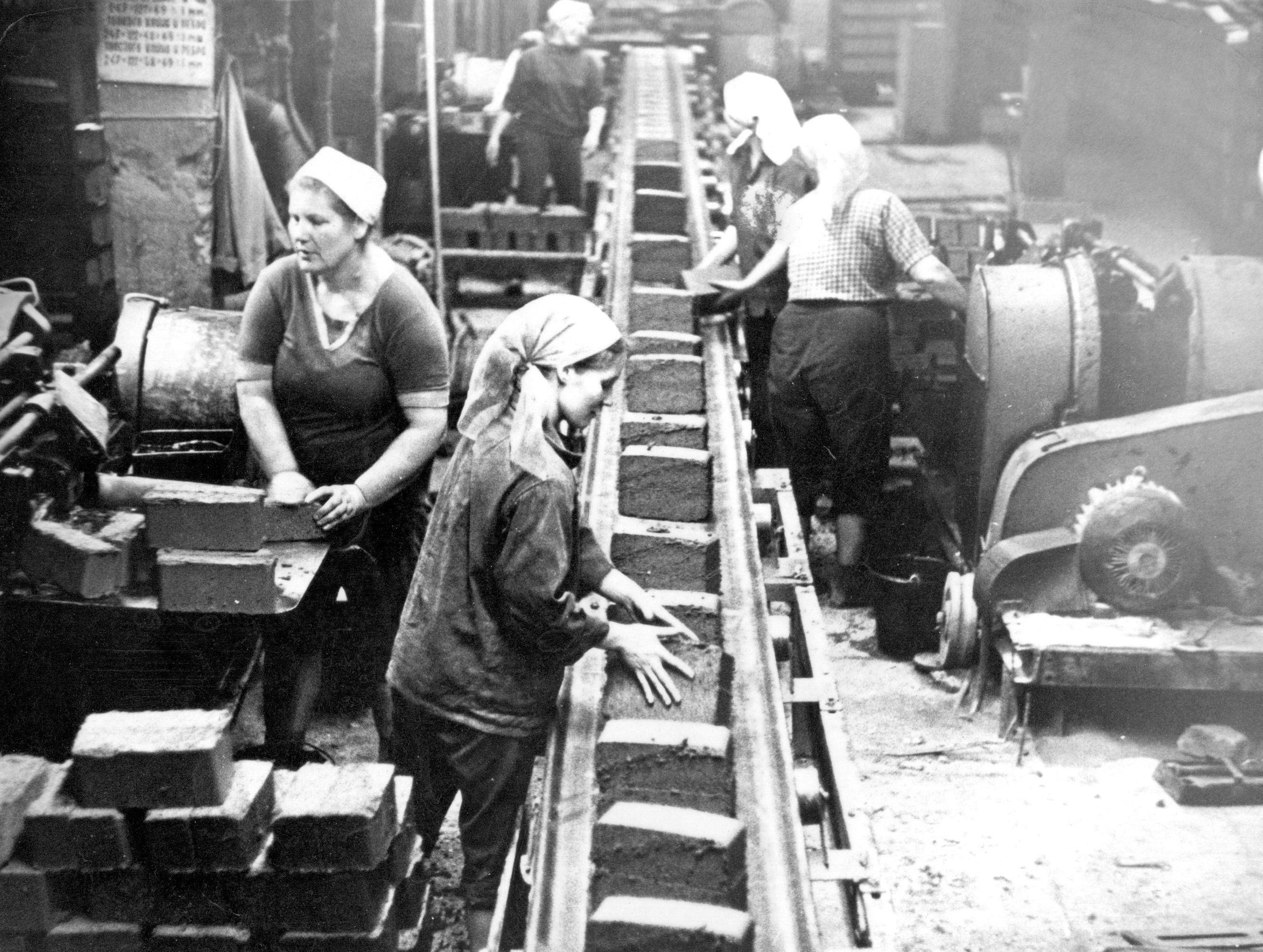
1956-1964
Over five years, the production of Sukhoy Log refractories increased by over 1.5 times (amounting to 1,106.2 thousand tons), the cost of production was reduced, and the production of new types of products was mastered. Improvements in production and technology continued. The drying drum No. 4, ball mill No. 4, tunnel dryers, and semi-dry pressing lines were put into production. The construction of the 3rd clay flow line with two disintegrators was underway.
A new mechanical shop and a plant boiler house were erected. In 1962, a complete reconstruction of the grinding and crushing department was carried out, a semi-dry pressing shop was put into operation, and the gas furnace (calcinating) shop with tunnel kilns was completely upgraded.
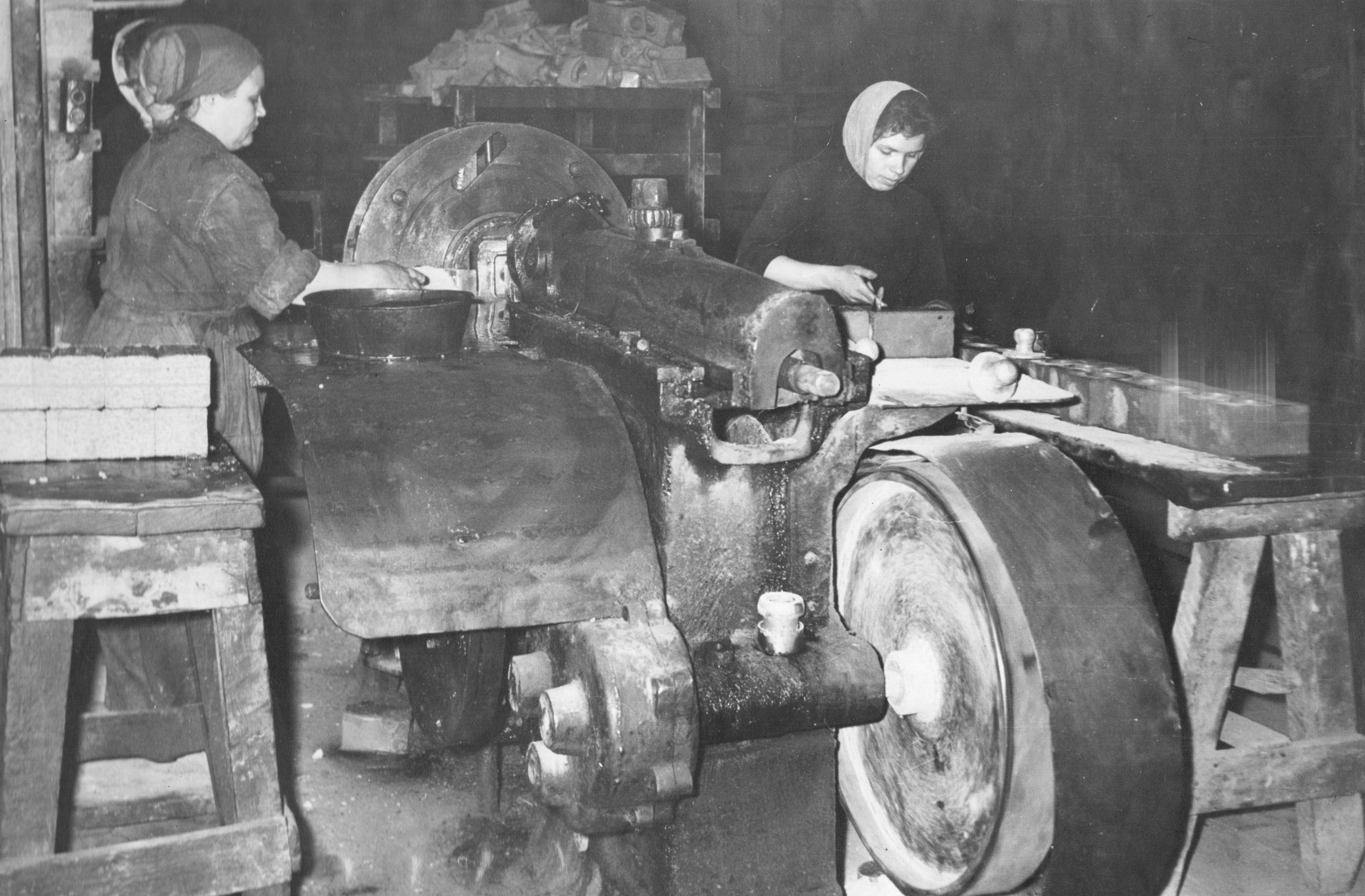
1965-1970
In the mid-60s, an economic reform took place in the USSR, where new planning indicators were introduced: plan of profits, profitability, and return on assets. To move to a new economic reform, production was reoriented towards more profitable products: an increase in the production of bottom cast products, lightweight products, exceptionally complex shapes, and ultra-lightweight products.
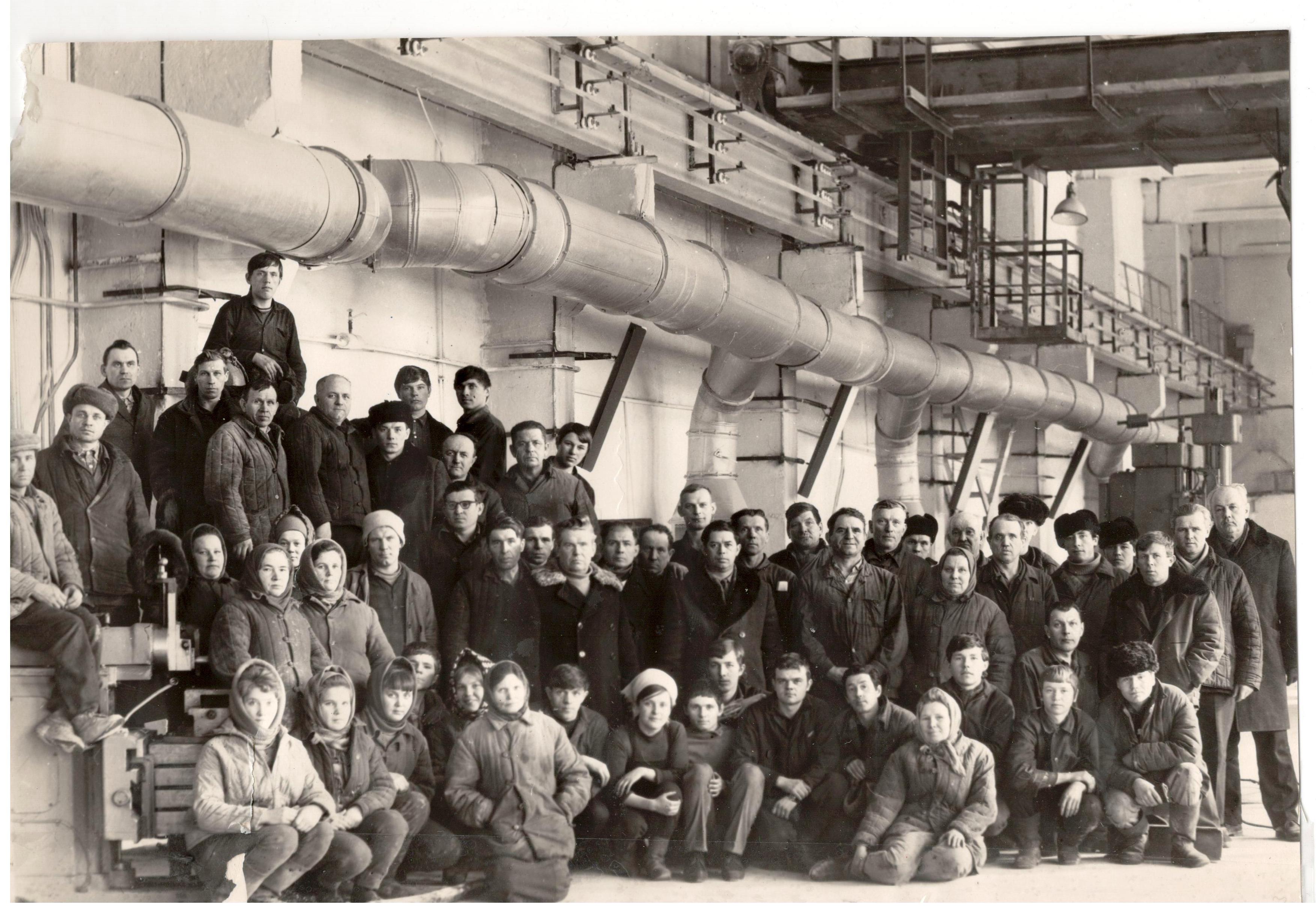
1970
During the eighth five-year plan, universal secondary education for young people was introduced in the USSR. The importance of vocational schools and technical colleges increased. If in 1932 the plant had only one engineer and three technicians, then by 1970 the plant personnel included 17 engineers, 214 technicians, 1,085 highly qualified workers (the total number of personnel at that time amounted to 1,733 people).
By 1970, the Sukhoy Log Fireclay Plant was one of the largest enterprises in the industry with an output of 241.4 thousand tons of refractory products per year.
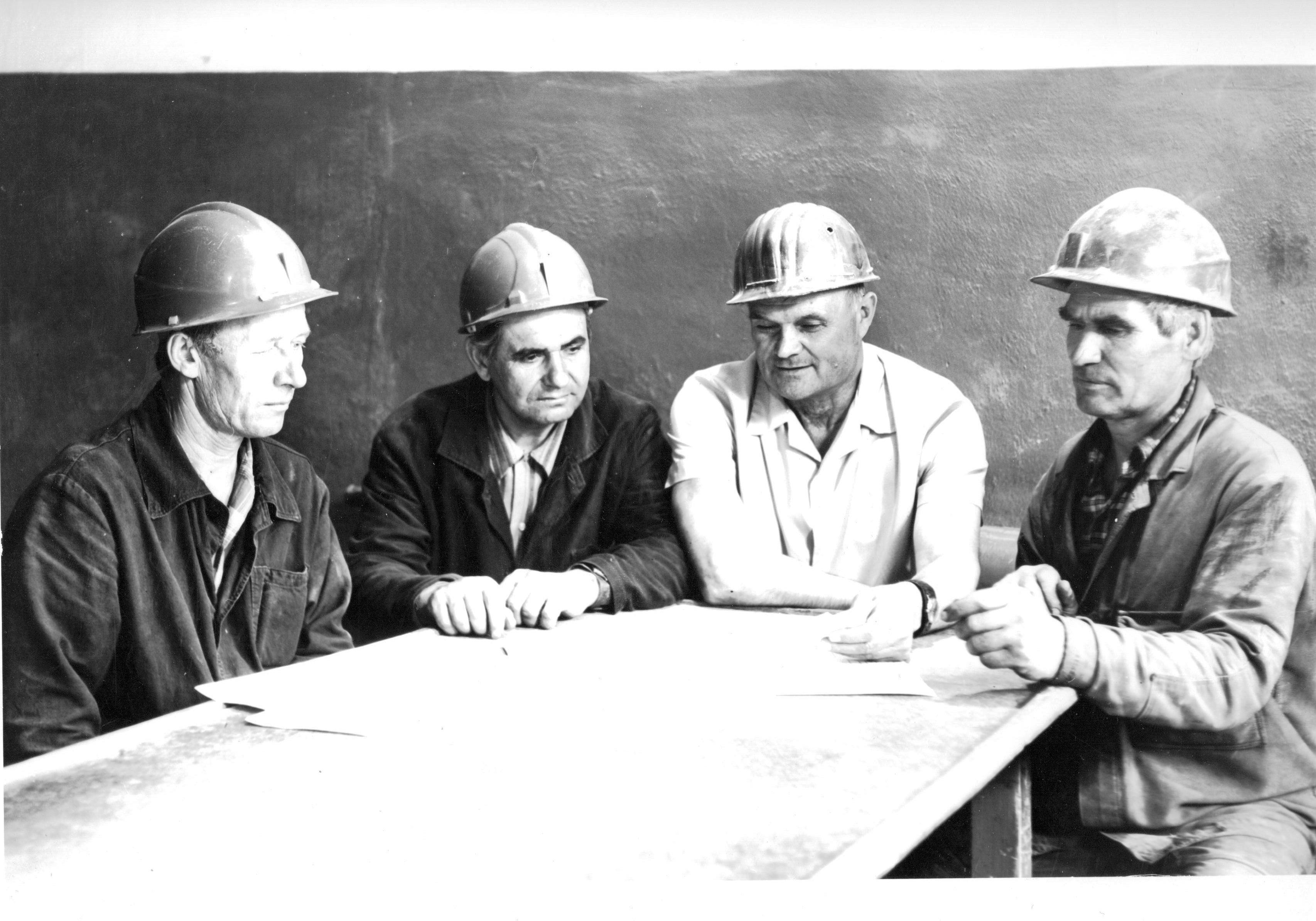
1971-1974
The Sukhoy Log Fireclay Plant was renamed the Sukhoy Log Refractories on February 1, 1971.
A fireclay crushing flow line with an elevator was installed and launched in the grinding shop. Electric vibrators and 25 powerful electromagnets for catching metal were installed on all clay and fireclay flow lines; at the bridge crane site, electric hoists were mounted, four switchboard rooms and a foreman's office were built.
In the gas furnace (calcinating) shop, the modernization of tunnel kilns continued, and a single electric carriage was put into operation for feeding empty stock to the loading area and loaded cars to kilns. In the press and moulding shop, the edge runners were replaced with mechanised ones with automated powder filling. In 1975, the ultra-lightweight shop was brought into service.
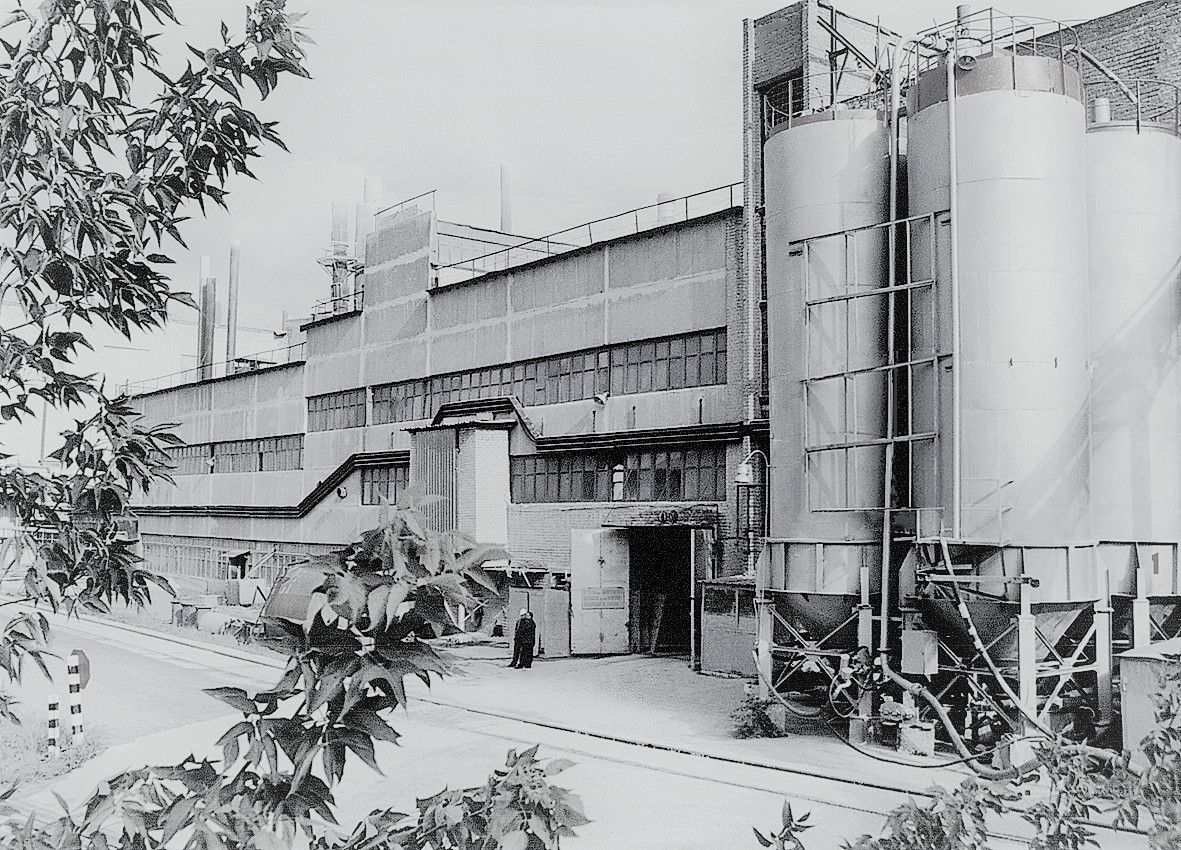
1974-1975
A distinctively effective direction in the plant development and its economy was the arrangement of industrial refractory glass fibre production. The shop was commissioned in January 1974. 1,302 tons of fibrous refractory material were produced, with a design capacity of 1,000 tons per year.
In 1975, due to improvements in production and technology, as well as mastering the continuous process, the design capacity of the furnace No. 1 for fibre production was exceeded. The same year, refractory fibre board production was arranged. These were shipped to the construction of the largest blast furnace in the world at the Krivoy Rog Steel Plant.
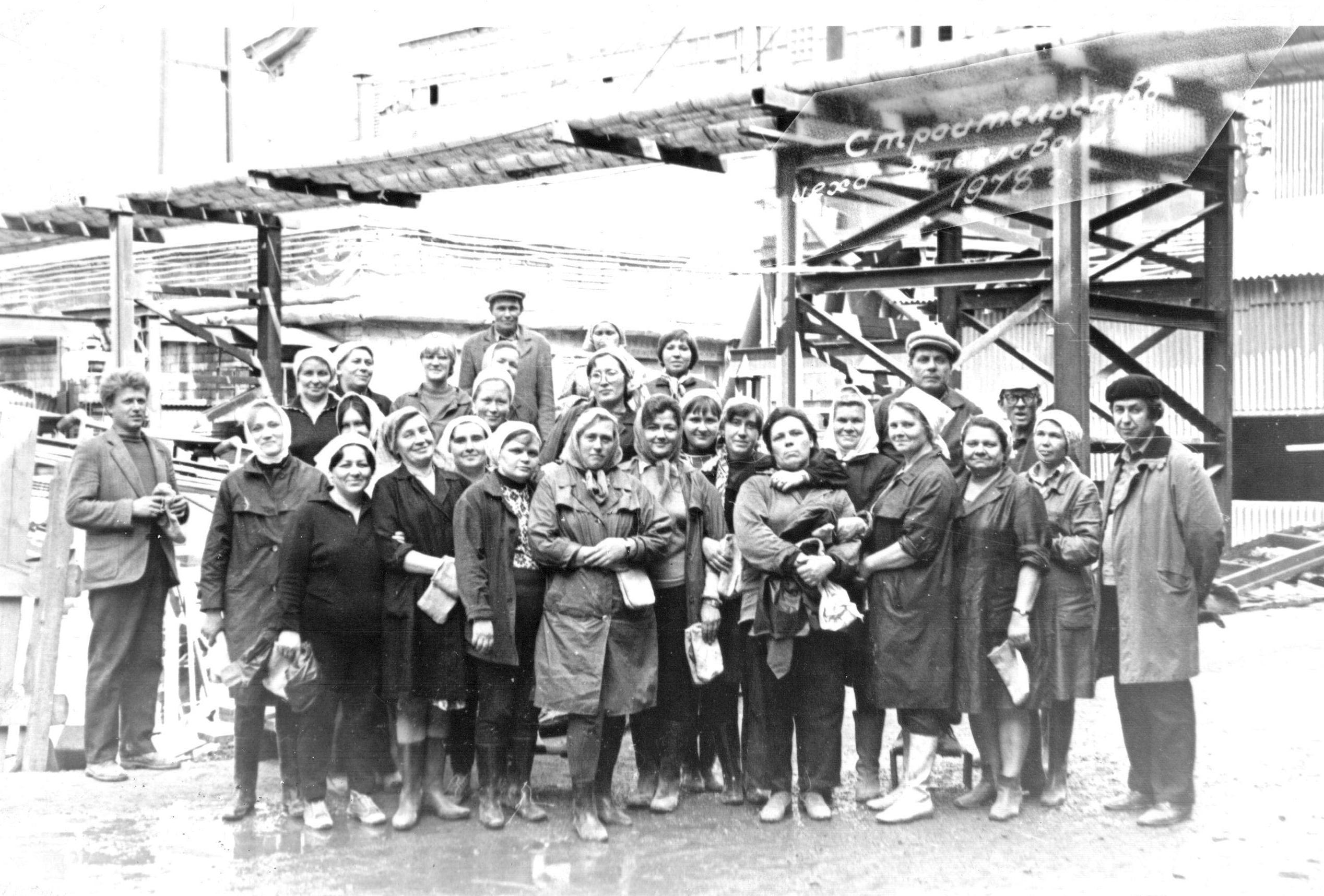
1976-1980
The manufacturing of fibrous materials and products in the glass fibre shop was growing at a swift rate. In 1977, the following amounts were produced: marketable fibre - 1,289 tons, boards - 996 tons, felts - 37 tons. In total, the shop produced 2,322 tons during the year. Mullite silica fibre was awarded the State Quality Mark. In December 1978, the second stage with the SKV-6098 ore-thermal furnace was put into operation.
Mullite silica fibre and related products quickly found their application, as these were in high demand by metallurgical plants and the military industry. Given the high demand for the glass fibre shop products, construction of the third stage was urgently commenced, which was commissioned in the shortest time possible and put into operation in December 1980.
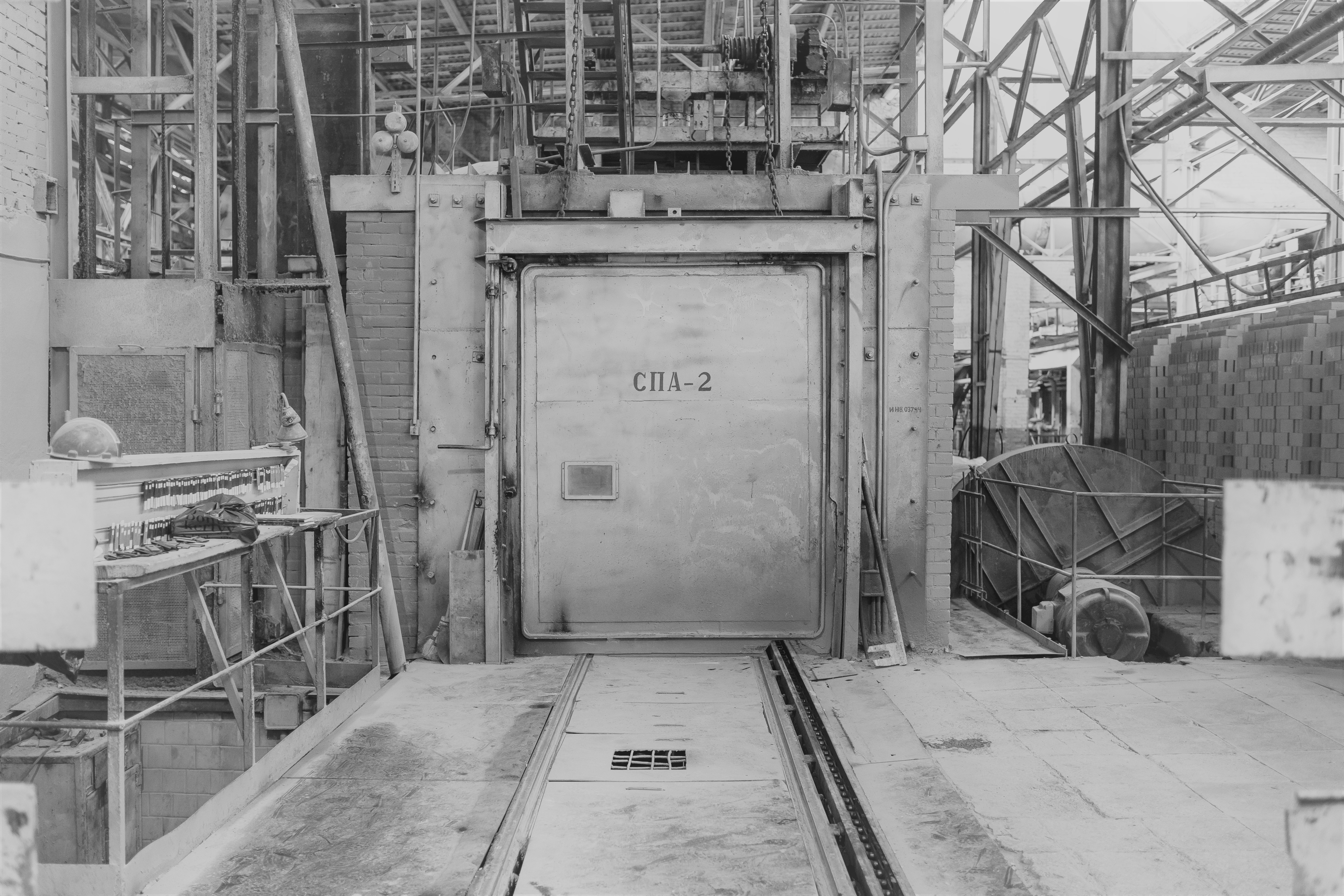
1981-1985
In 1981, a gas system was put into operation complete with a horizontal pumping unit for the calcinating shop and the 5th tunnel kiln. In 1982, the 4th tunnel kiln was converted to natural gas. In the press and moulding shop, the PK-630 were replaced with more efficient ones – SM-1085. A second pneumatic transport line was constructed to feed sawdust from a warehouse and an inclined gallery was installed to feed the mass to the press No. 5.
In the grinding shop, works were performed to convert four drying drums to natural gas, a gallery for feeding fireclay to ball mills and a jaw crusher section were constructed. The fireclay crushing department was put into operation, and the shop for producing lightweight products on a phosphate bond was built.
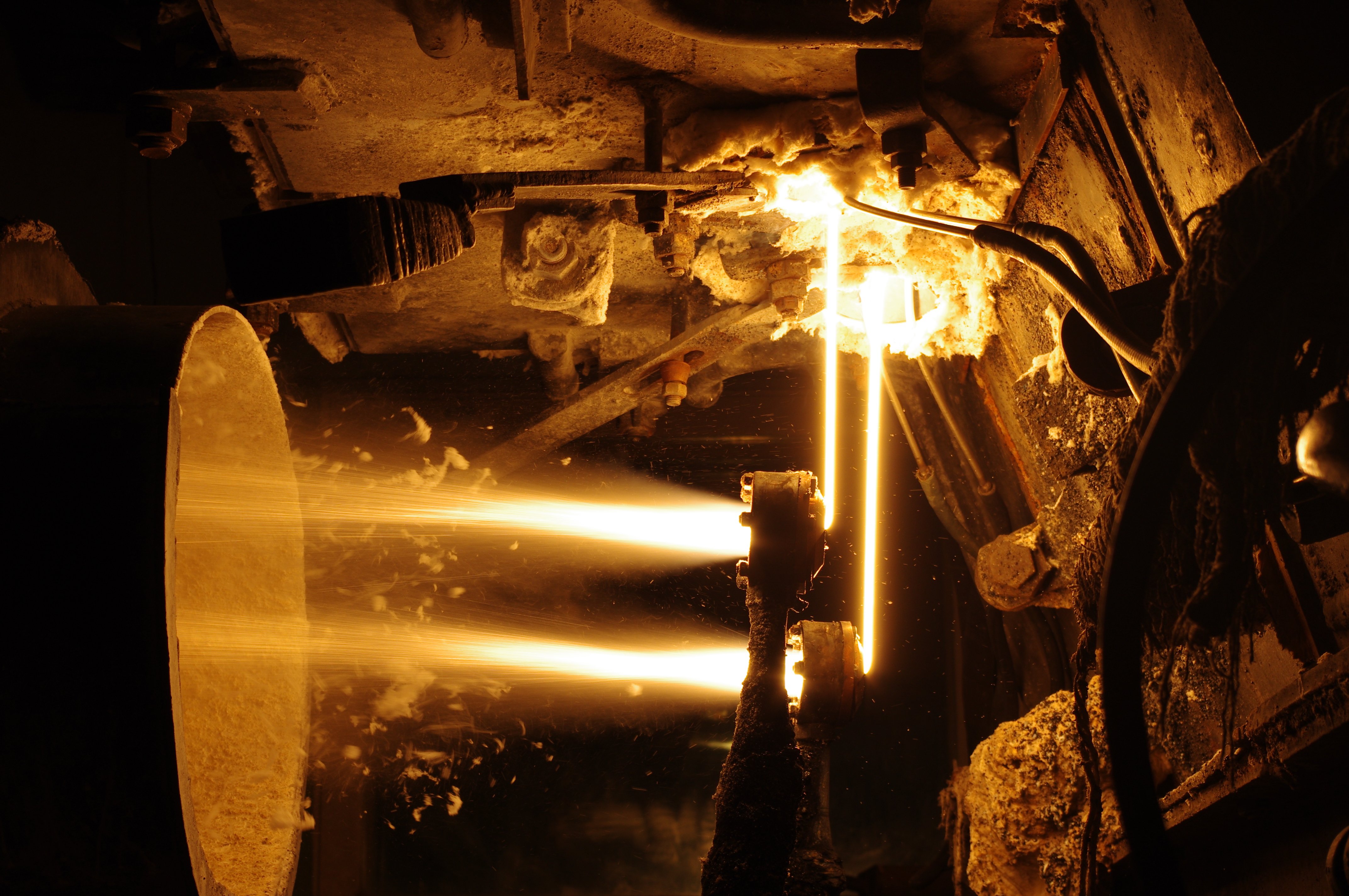
1986-1990
In the ultra-lightweight shop, a tank for receiving alumina through a pneumatic transport system was installed, and a warehouse for storing perlite sand was constructed. In the plastic pressing shop, additional equipment was manufactured and installed for the C-80 and C-88 complex bottom cast grades production.
In the glass fibre shop, under the most challenging conditions, the old electric arc furnaces were dismantled and replaced with new and more efficient dual-jet blast furnaces. Works on technical re-equipment and expansion of the glass fibre shop almost doubled the production of refractory fibre and products based thereon by 1990.
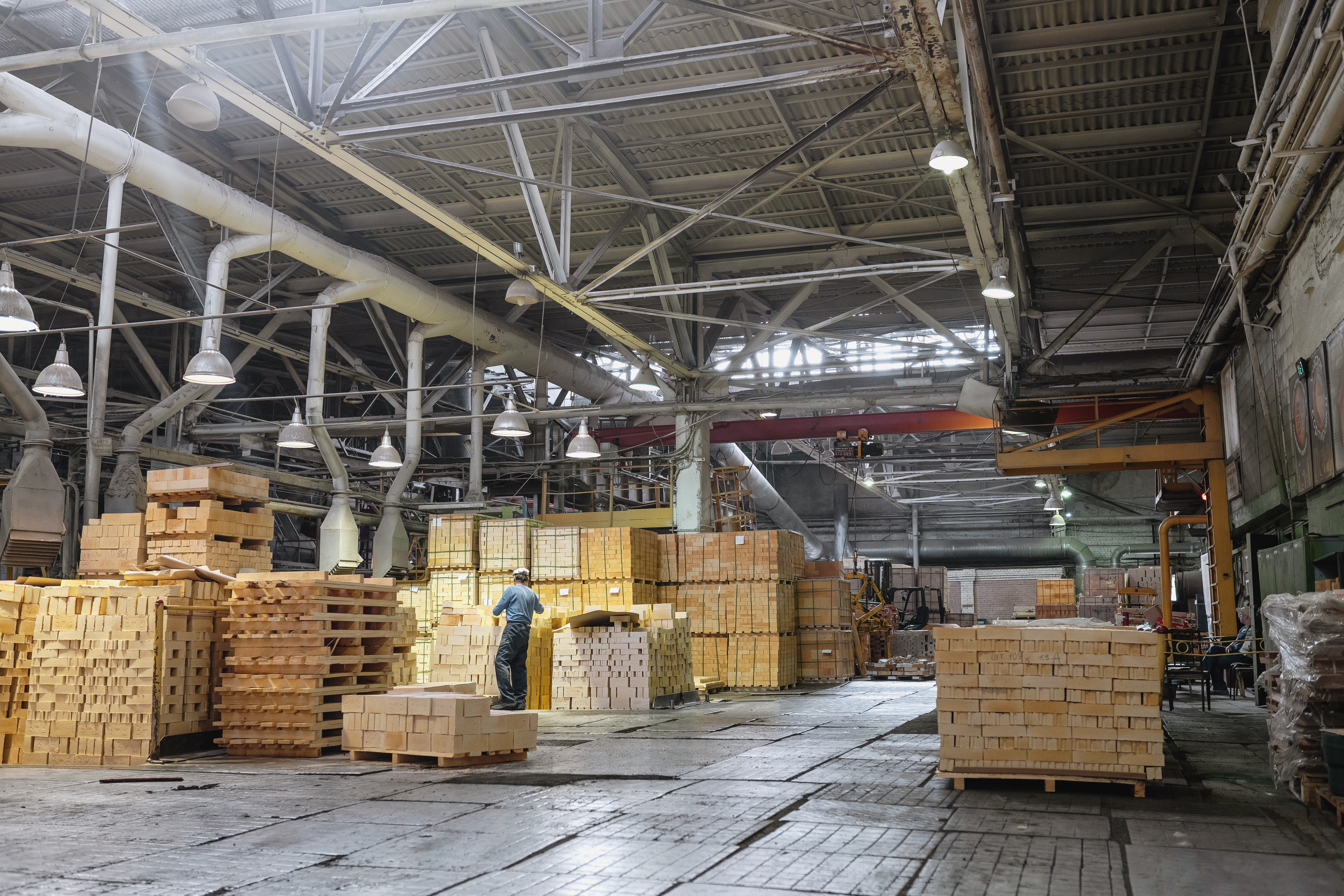
1993
The Sukhoy Log Refractories were transformed into the open joint-stock company on October 25, 1993. By that time, the plant supplied casting pit refractories to 13 metallurgical plants. Lightweight refractory thermal insulators were shipped to 600 enterprises across the country, and 1,500 enterprises received fireclay refractories.
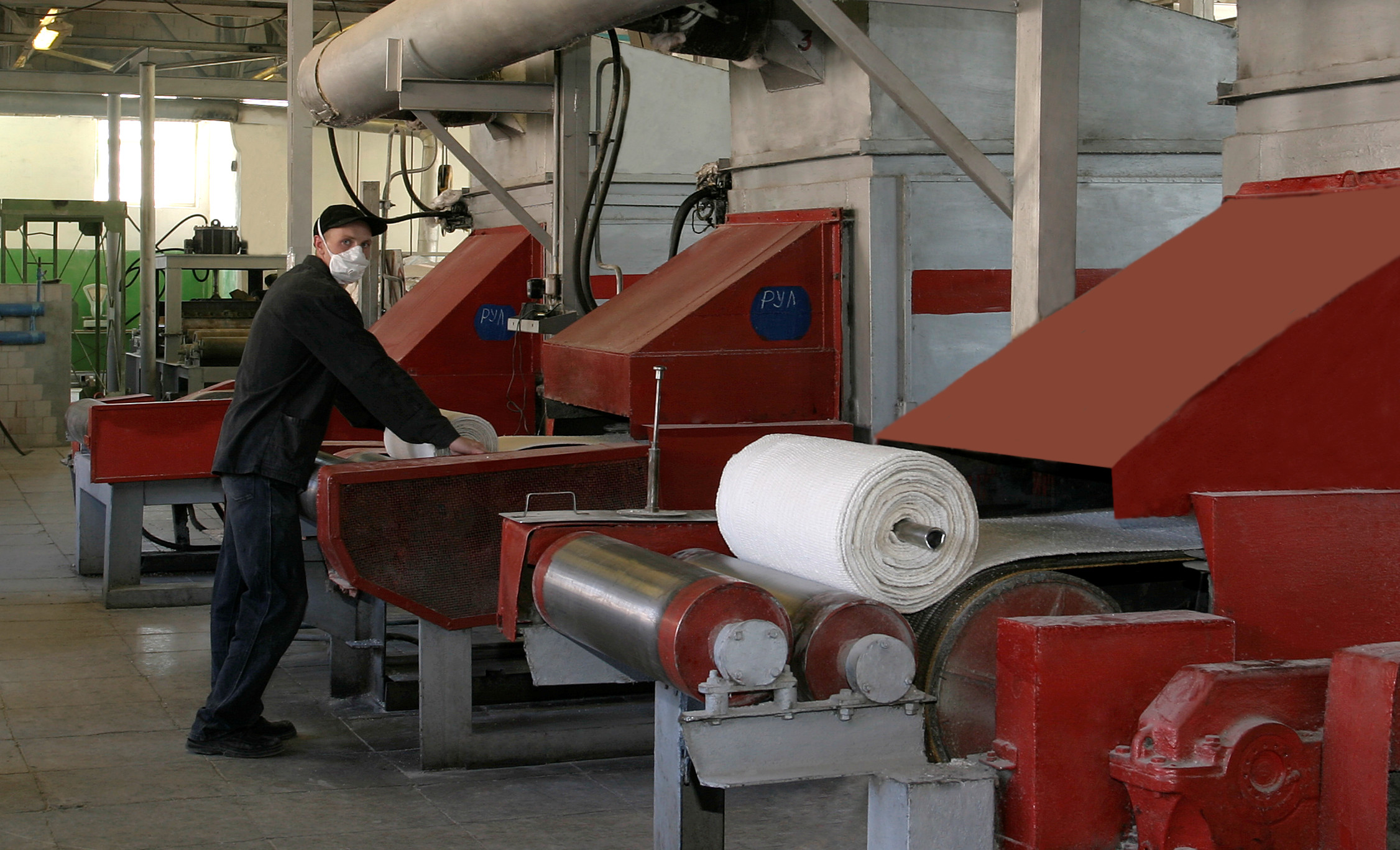
1995-2001
Through this period, the plant’s personnel managed to increase the output of refractory cardboard and complex configuration products made of refractory fibre many-fold due to the technical re-equipment of the products section. A large-scale reconstruction of the grinding shop was completed, which enabled organising large-scale production of unmoulded refractories.
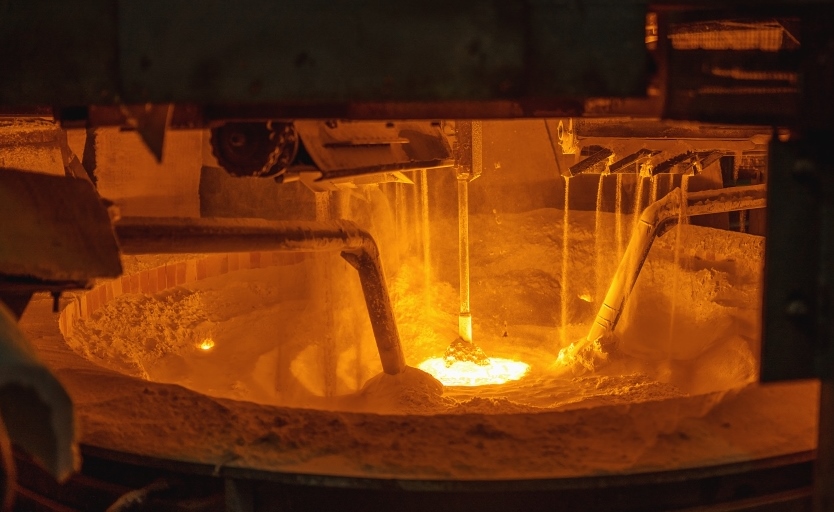
2006
In 2006, on the basis of the Sukhoy Log Refractories OJSC, which was one of the largest manufacturers of fibrous mullite silica materials and products based thereon in Russia, a joint venture, Morgan Thermal Ceramics Sukhoy Log LLC, was established with Thermal Ceramics, the world leader in ceramic fibre thermal insulation production.
A new process line for the production of refractory ceramic mullite silica glass fibre using the centrifugal method was installed and commissioned. The estimated line capacity is 3,500 tons/year.
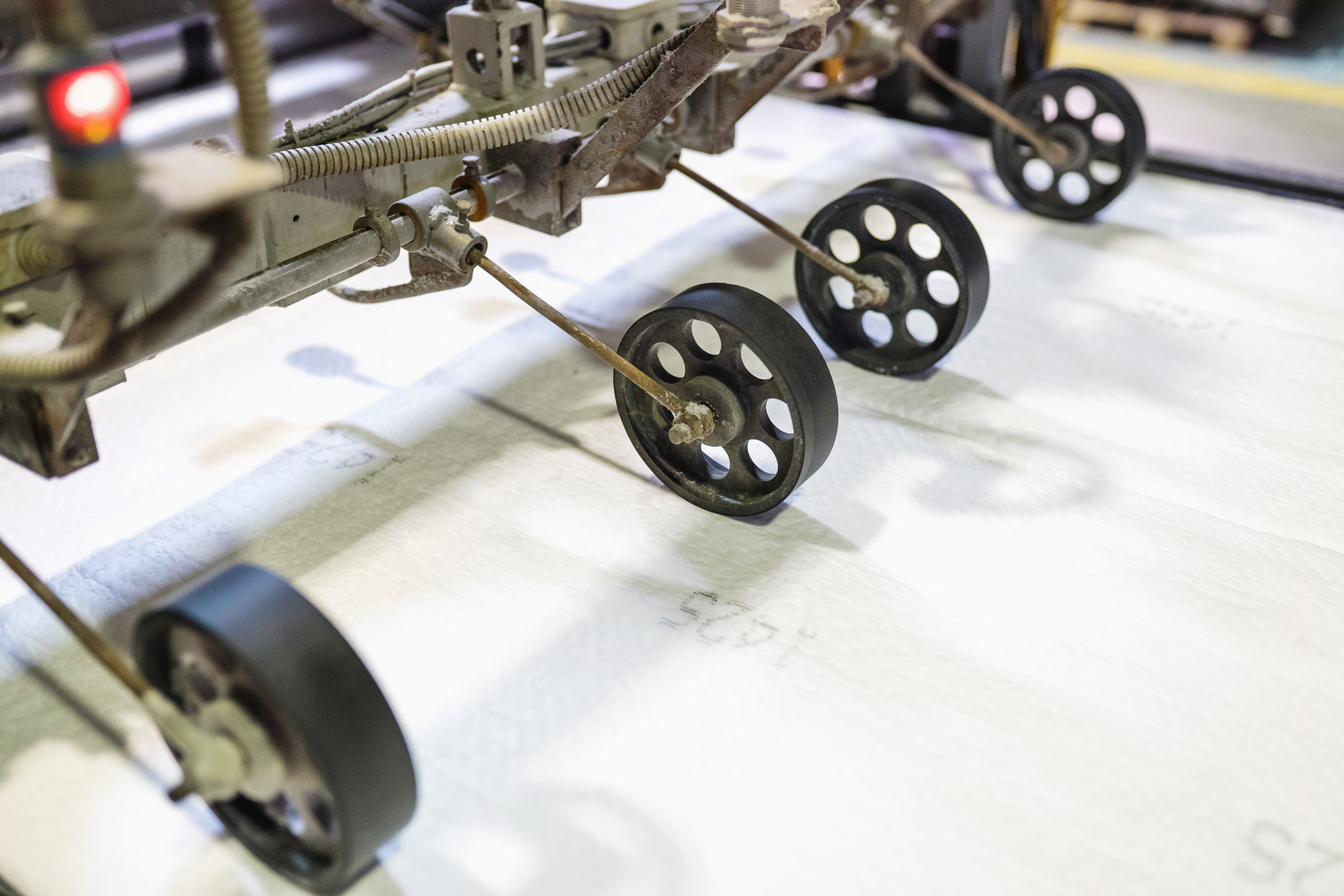
2009
The technology for producing refractory ceramic glass fibre was elaborated. The line was officially launched in May of the following year. The line for producing rolled materials was designed and built with a high level of automation of all processes, from charge preparation to cutting of finished material.
All stages were subject to video and electronic monitoring with 400 parameters recorded on a computer every 20 minutes. A high degree of process automation enabled obtaining materials with specified parameters that fully complied with the global quality standard of Thermal Ceramics.
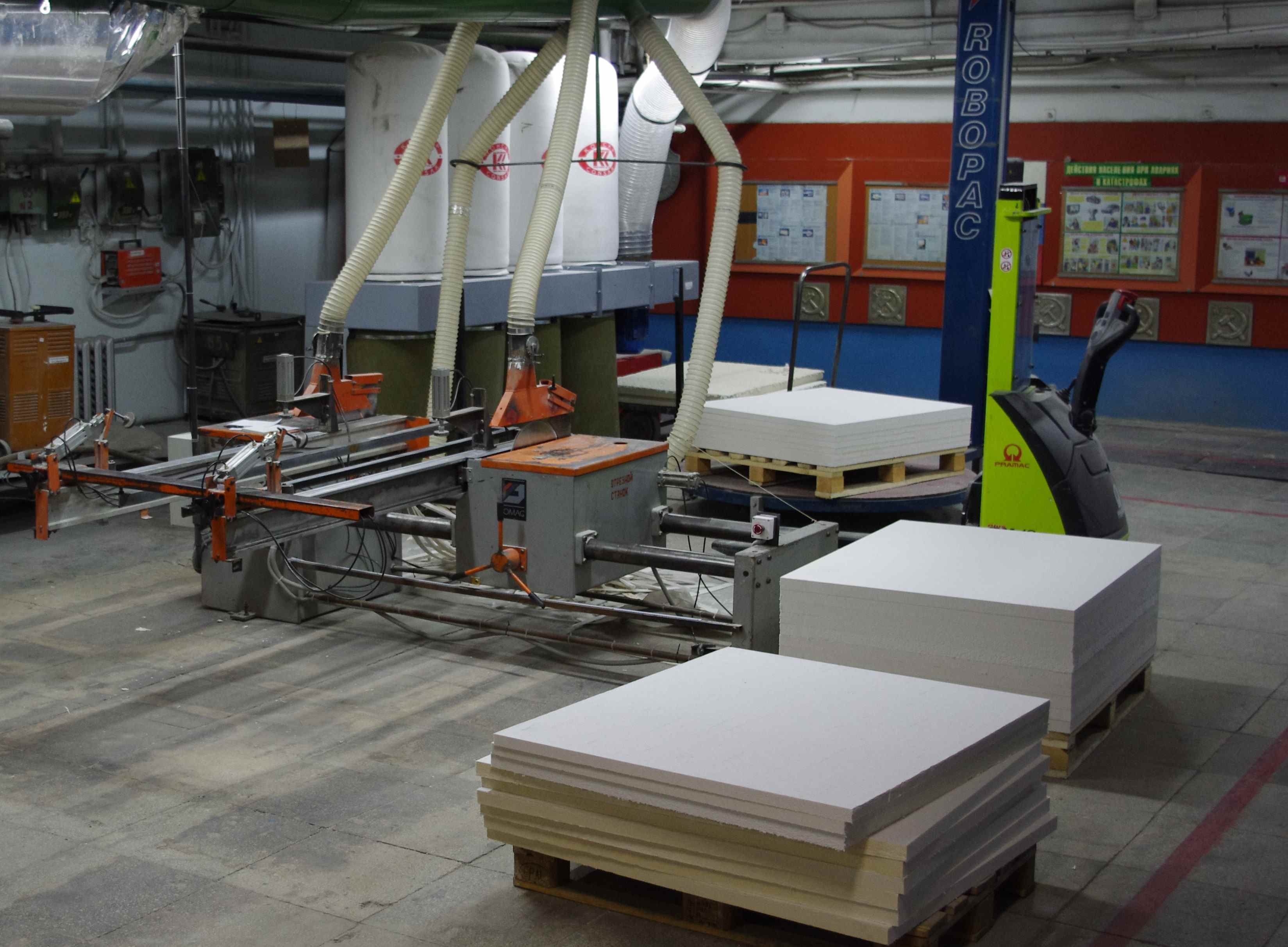
2011
In the first half of 2011, installation works were completed and the technology for producing vacuum-formed, large-format thermal insulation boards as per Thermal Ceramics technology was elaborated.
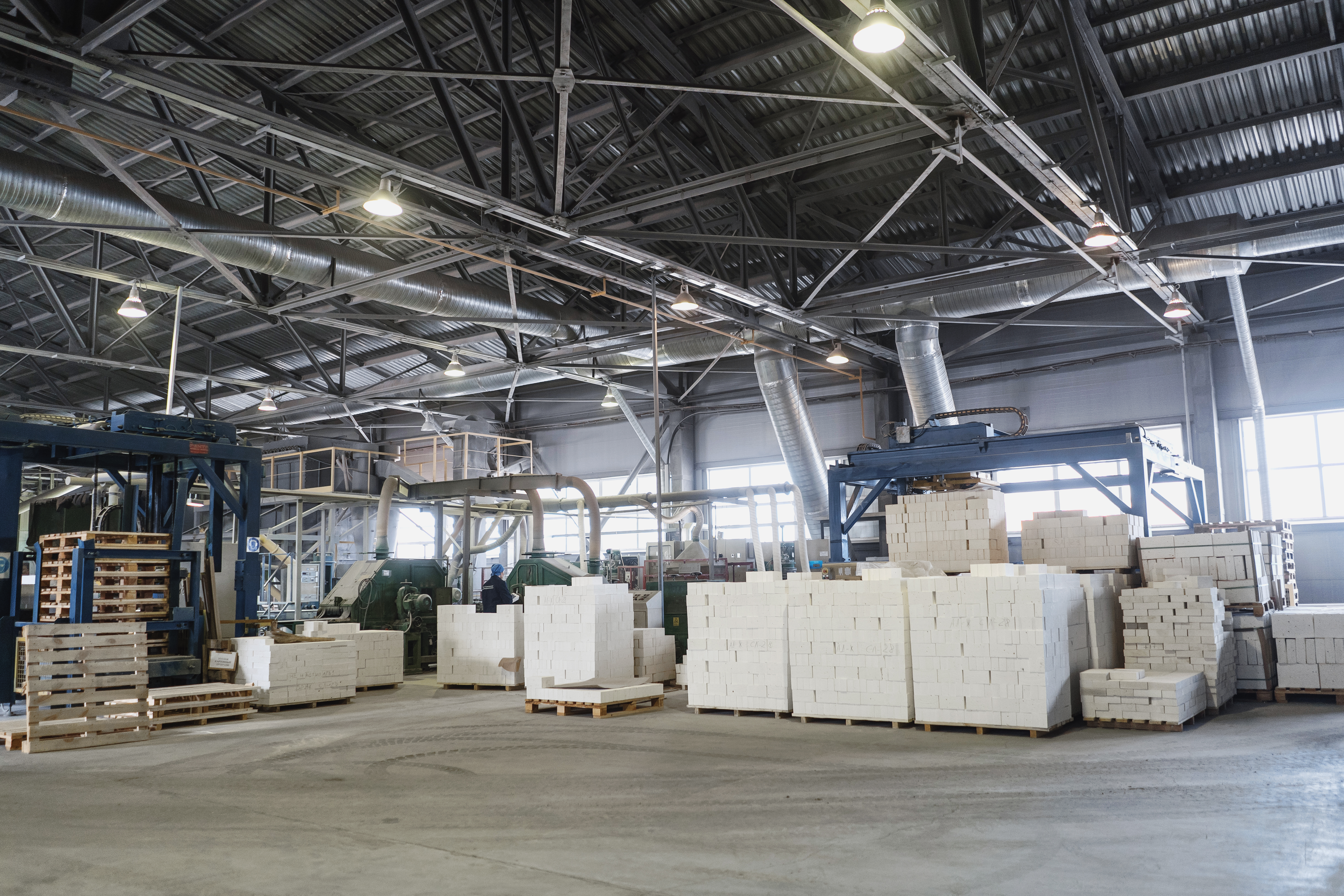
2013-2014
In 2013, the Sukhoy Log Refractories acquired one of the leading Italian companies producing thermal insulation products and unmoulded refractories - NUOVA ISOLTERMICA. By 2014, all production lines were moved to Russia.
The technology for producing a completely new grade of thermal insulation products called SL was elaborated. SL 23, SL 26, SL 28, SL 30 products comply with the ASTM international standard and can be used in thermal insulation layers of linings made according to the designs of leading international engineering companies.
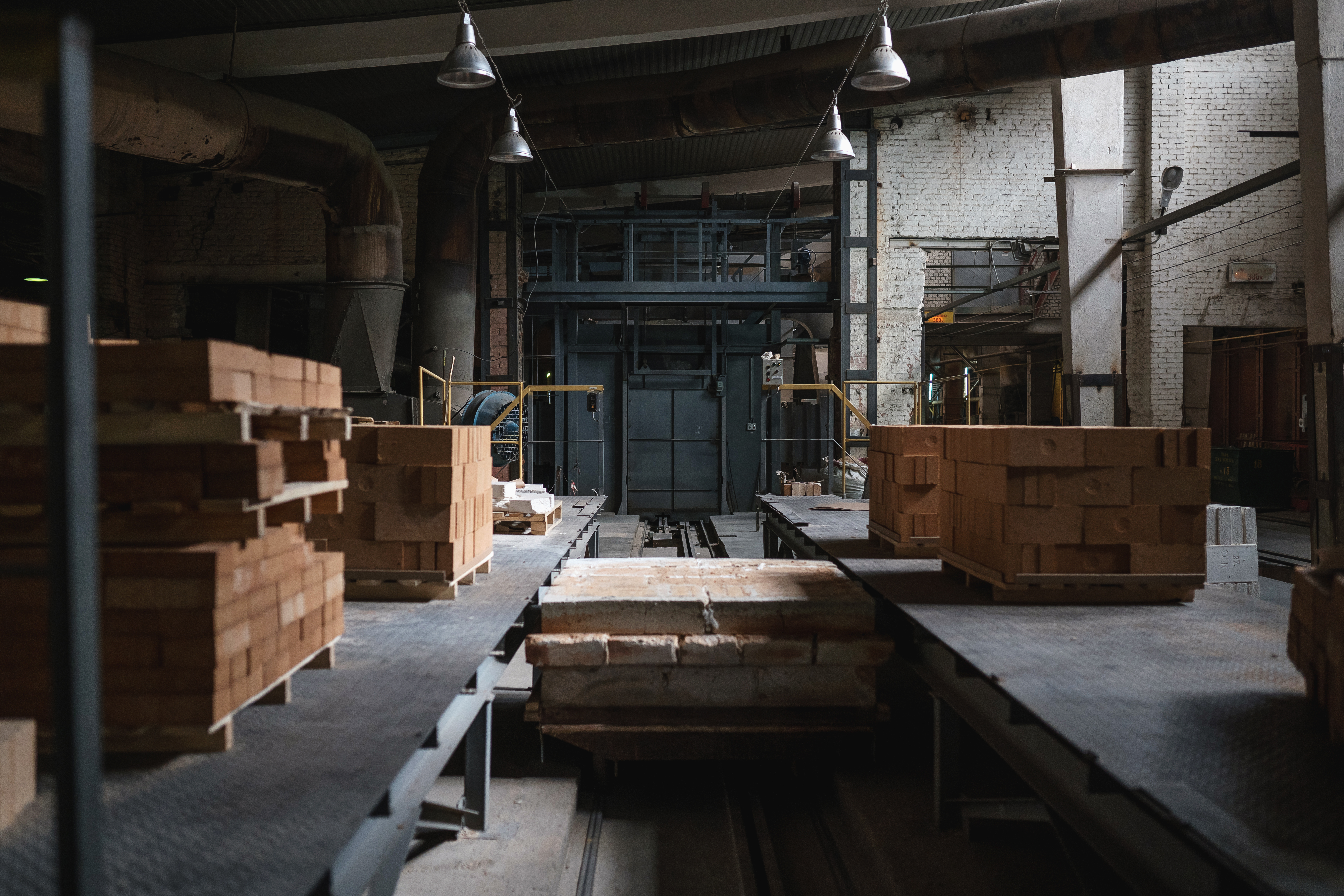
2015
A new tunnel type furnace N1 of the molding and calcination bay was put into operation on 1 June 2015. Sukhoy Log Refractories OJSC launched the industrial production of moulded high-alumina and corundum refractory and thermal insulation products.
The production of unmoulded refractories and dry refractory concrete mixtures was scaled up drastically.
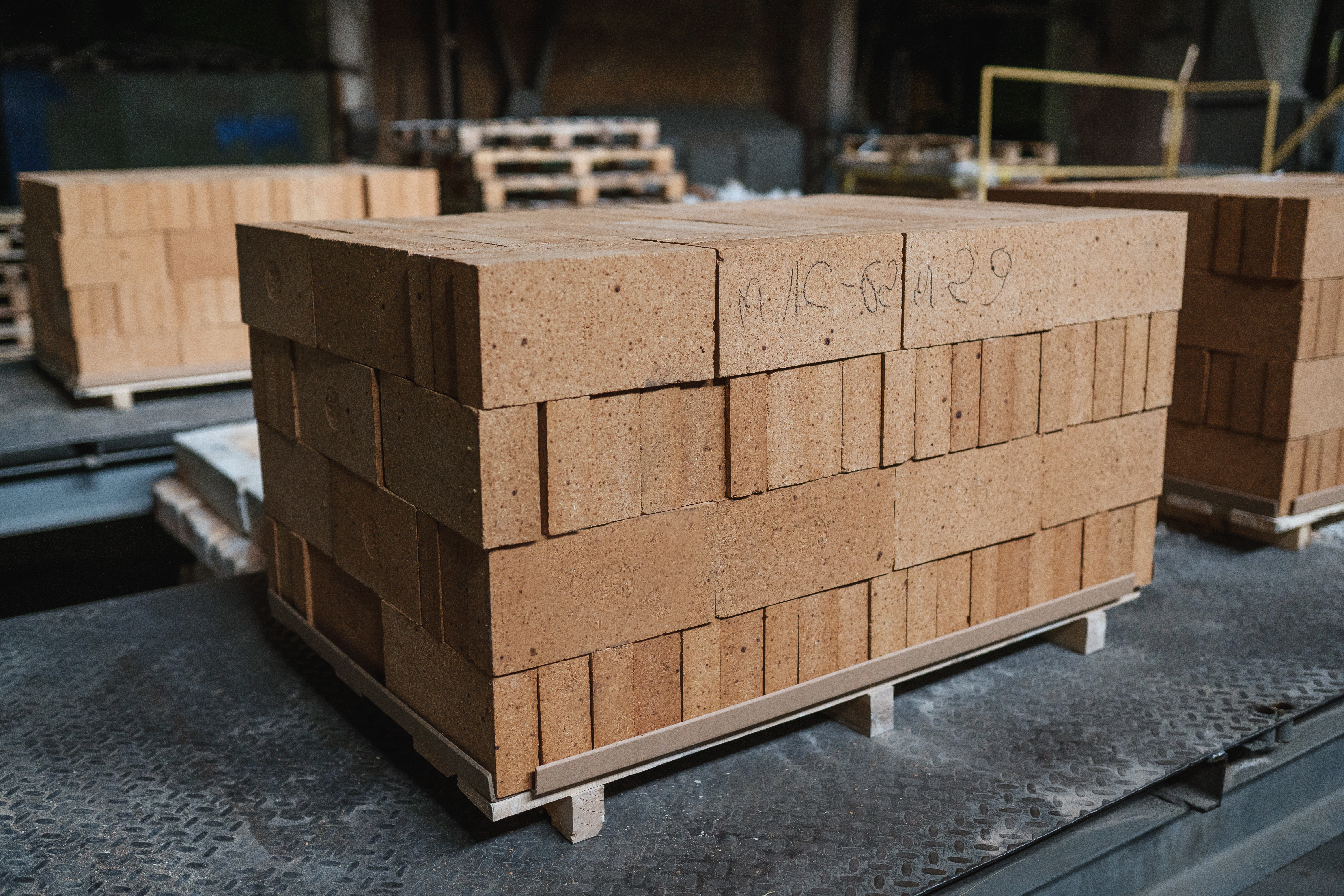
2016-2020
The range of moulded dense refractories produced was significantly expanded. The following grades, completely new for the enterprise, were mastered: MKRS-45, MKRU-45, MKRP-45; MLS-62, MKS-72, MKU-80; MKS-90, KP-95, KS-95, KU-95; packed products for air heaters of ShV-37, ShN-38, ShV-42, and MKRN-45 grades.
The range of thermal insulation refractory products was expanded. In addition to the plant’s traditional products of the ShT (from ultra-lightweight 0.4 to 1.3) and MKRT (0.7-0.8) grades, a significant share of the manufactured products was made up of MLT-1.3 grade products. In addition, upon successfully elaborating the technology in laboratory conditions, the enterprise was preparing to produce a pilot batch of corundum thermal insulation products of the KT-1.1 and KT-1.3 grades.